Breaking barriers: Researchers analyze how a chemical process could help recycle a common plastic waste
The work suggests key areas for researchers to focus on in order to meaningfully advance PET recycling and allow new recycling technologies to be commercially feasible.
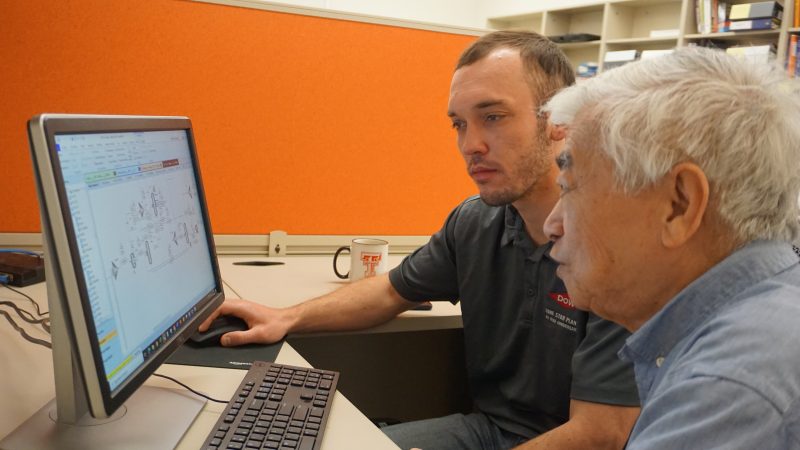
Researchers at Virginia Tech are exploring processes that might greatly increase the recycling of one of the world’s most-produced plastics.
Published in the Feb. 12 and 16 issues of the Industrial and Engineering Chemistry Research, Ph.D. candidate Adam McNeeley and his advisor, Alumni Distinguished Professor Y. A. Liu, a member of the Macromolecules Innovation Institute, report their investigation of chemical recycling processes that remove additives, impurities, and colorants from polyethylene terephthalate, commonly referred to as PET. The processes can allow for a greater percentage of the plastic to be recycled than with the current mechanical recycling processes.
PET is found in many everyday use items such as textiles, packaging, and bottles. Current recycling of it is primarily done via the mechanical process, which is limited to clean recycled materials and is mostly applied to plastic bottles. Plastic bottles only make up about 30 percent of its end use, and the other 70 percent is not generally being considered for commercial recycling.
“The importance of this research is to identify and develop the cheapest and most efficient ways to recycle PET,” said McNeeley, who is studying chemical engineering, “There is a clear public desire to use products made from recycled materials, but if the recycled material costs a lot more than the virgin material, then people are less likely to buy the recycled material.”
McNeeley and Liu investigated depolymerization pathways using ethylene glycol, methanol, or water to produce monomers that can be purified of additives, impurities, and colorants in plastic waste and then converted back into recycled PET polymer. Prior to their study, most of the work related to the chemical depolymerization of PET focused only on the chemistry aspect. But this research provides a thorough assessment of thermodynamics, chemistry, purification, waste management and sustainable design of PET depolymerization processes.
The research team created a complete simulation model of four depolymerization processes that quantify the mass and energy balances together with energy demand and carbon dixoide emissions, which is a quantitative foundation for industrial practitioners interested in its depolymerization to further develop sustainable depolymerization processes.
“There are many different ways PET can be depolymerized and there are three that are being actively developed for commercial use, and we demonstrate how these different methods compare from a chemical processing standpoint,” McNeeley said.
Their work also suggests key areas for researchers to focus on in order to meaningfully advance plastic recycling and allow new recycling technologies to be commercially feasible.
“One of the greatest challenges with mechanical recycling is that certain dyes and impurities cannot be removed,” McNeely said. “A lot of effort must be made in the sorting and cleaning of waste PET that can be mechanically recycled. Converting the polymer to a monomer opens up a number of purification pathways and allows waste PET of theoretically any quality to be recycled. It also opens up the possibility to recycle other PET materials such as packaging and textiles, which actually comprise the majority of PET end use.”
There are many companies actively developing PET chemical recycling technologies, one of which is Eastman Chemical Co. Eastman has built the first large-scale depolymerization unit in the United States using methanolysis in Kingsport, Tennessee.
“It is important that traditional chemical companies such as Eastman are working on this technology. These companies have access to large amounts of capital to build large-scale processes and have the know-how and experience to develop and operate processes efficiently and reliably, which is important for emerging recycling technologies to survive especially during turbulent market conditions,” McNeeley said.
“This is a timely and significant, thought-provoking study,” said Joseph Bays, the licensing technology manager of the company. “I am a fan of the heat integration innovation to save energy consumption, and some other innovative features of the sustainable design study."
Given the global context of PET recycling, McNeeley said such efforts should carry with them a level of urgency.
“Plastics are currently derived from fossil fuel-based feedstocks. Fluctuations in plastic prices and relatively low prices of fossil fuels tend to kill plastic recycling efforts because it is hard to make money,” he said. “There is a finite amount of fossil fuels and prices will eventually rise as the resource becomes more scarce. This is where plastic recycling efforts become reliably profitable, while preventing plastics from becoming extremely expensive as we transition to using non‑fossil fuel derived feedstocks”
The published article was honored as the Editors’ Choice Article for Feb. 16 by the American Chemical Society, which publishes Industrial and Engineering Chemistry Research. The Editors' Choice initiative highlights one article each day for its timelyness, public interest, and potential impact.