Virginia Tech’s Orbital Launch Vehicle Team celebrates successful launch in California
Editor’s note: With Virginia Tech Giving Day 2022 beginning at noon Feb. 23, a series of stories highlighting the impact of donations are featured on VTx this month.
In business terms, taking a “30,000 foot view” means stepping back and gaining a high-level, big-picture perspective on a project or challenge. The metaphor also fits the Orbital Launch Vehicle Team (OLVT), a Virginia Tech student design team that has learned to slow down, move forward from past missteps, and take the time needed to build toward its long-term goals in measured, incremental steps.
While some student design teams work all year long toward an annual competition, the OLVT team has loftier, long-term aspirations in sight. For several years, team members have worked continuously to progress technology on their launch vehicles and advance opportunities for student rocketry and small satellite teams in hopes of becoming the first collegiate organization to deliver an object into low Earth orbit.
The team recently moved one giant step closer, with a successful launch of its current subscale test rocket in the Mojave Desert.
Test Turkey
Over the past five years, the OLVT team has progressed toward its goal of crossing the Kármán line and putting a rocket into orbit. As the team works toward developing the Hokie 1, its future orbital launch vehicle, numerous small-scale rockets have preceded it. There was the Hokie 0.25, a small one-stage rocket that reached 5,000 feet at Kentland Farm in 2016; and the Hokie 0.50, a two-stage rocket that launched to 17,000 feet in 2017 in Argonia, Kansas. With each iteration, the future engineers have gained hands-on experience in design, fabrication, and flight testing.
The OLVT team’s current focus centers on the Test Turkey, a subscale test rocket approximately 89 inches in length and weighing about 40 pounds loaded, or 20 pounds once the motor has burned. The Test Turkey is a smaller-scale model of their next planned large rocket, known as the Hokie 0.75, and has been fabricated with an aluminum and fiberglass body that houses a commercially manufactured N-1000 solid motor.
It’s been a long two years since this team has attempted any sort of large-scale launch. During this period, the OLVT team has taken its time to develop and iterate a number of technologies on Test Turkey, striving to design and fabricate the cleanest, safest, and most effective launch vehicle possible. Team members rigorously verified their designs, regularly meeting with their faculty advisors and gathering input from industry experts.
Using the maker space at the new Advanced Engineering Design Lab (AEDL) and the airstrip and hangar at the Kentland Experimental Aerial Systems Laboratory, the team tested major design elements and systems and then adjusted as necessary. With each smaller test and refinement of the on-board systems, the OLVT team steadily inched closer and closer toward launch readiness and setting a launch date.
This past semester, the team specifically focused on developing an efficient recovery system, or parachute ejection system. According to Reece Preisser, a senior majoring in physics and OLVT co-president, this proved to be one of the most elaborate parts of building the rocket. “In space, we’ll need to use CO2 cartridges to eject, and it’s important that we learn how to properly deploy that system at any altitude for a safe recovery. With a good system in place, we’ll be able to successfully recover this rocket, or an even larger-scale launch vehicle down the road.”
Leading up to the launch, the team also experimented with a new fin attachment method, bolting the fins into the body horizontally and machining the motor casing straight out of a big block of aluminum. The team felt motivated to push certain components to their limits, and test to see if they would work at a larger scale.
“We wanted to push this rocket as fast and as high as we could while also pushing the teams’ capabilities in terms of recovery, flight, and prediction of altitude,” said Preisser. “More importantly, throughout the process, team members were gaining valuable hands-on experience and becoming familiar with those technologies.”
The student team members meet weekly with their advisors, professor Kevin Shinpaugh of the Kevin T. Crofton Department of Aerospace and Ocean Engineering and assistant lab manager Bob Schoner of the AEDL. During these sessions, the students update the advisors on their progress, receive advice, and double check their next steps to ensure they are moving in the right direction.
“Our goal is to guide the students and assist them throughout each major phase of development,” said Schoner, who has been involved with high-power rocketry since 1995 and serves locally and nationally as a mentor and advisor on level 3 rocketry projects. “We don’t want to prevent them from making mistakes, but encourage them to fail early and fail small. By learning from these small and inexpensive mistakes, we’re helping them to avoid failure when the stakes are much higher.”
With six months to go prior to the launch, the team began working on finding a launch site and making its final preparations on the Test Turkey.
Trip to the desert
Depending on the scale and magnitude of any amateur rocketry flight, finding a launch site can be complicated. While the OLVT team is able to perform small-scale tests at nearby Kentland Experimental Aerial Systems Laboratory, the sheer size of the Test Turkey and its projected altitude would require the launch to be executed in a vast open space, far from civilization.
The team predicted that the Test Turkey would fly to an altitude approaching 50,000 feet. Because the Federal Aviation Administration requires waivers to fly high-power rockets weighing more than 3.3 pounds and flying on greater than 4.4 ounces of propellant, potential launch sites for the Test Turkey proved to be limited.
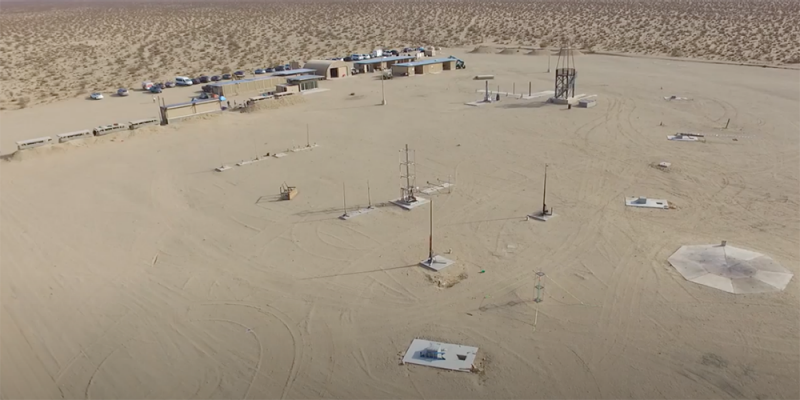
Working with the Friends of Amateur Rocketry organization, a not-for-profit organization providing infrastructure for testing and launching large amateur and experimental rockets, OLVT applied to launch the Test Turkey before the Thanksgiving holiday. The organization’s test and launch facility is located in California just north of Edwards Air Force Base and near the Mojave Desert. With the site’s strict safety regulations and higher launch ceilings, it quickly emerged as one of the only organized and viable places to launch the Test Turkey.
After its application for a launch window and official paperwork was submitted and approved, OLVT’s next hurdle would be organizing transportation for both the team and its gear. In addition to Schoner, the team would need 20 essential participants onsite to set up the rocket on launch day.
Most of the team would be able to book commercial flights to California, but members would still need to tackle logistics for transporting the rocket itself. Rocket motors contain high-energy propellant and pyrotechnic materials, and are therefore classified by the U.S. Department of Transportation as hazardous materials. Shipment of these motors is subject to detailed federal regulations and a lot of red tape. These items are also strictly forbidden to be carried or shipped as cargo on passenger-carrying aircraft.
With the help of the aerospace and ocean engineering department, the OLVT team rented a large truck and borrowed a 12-foot trailer from fellow undergraduate design team Rocketry at Virginia Tech. Four of the essential OLVT team members volunteered to make the three-day cross-country trip to tow the trailer with rocket and launch gear out to California, and four different members would make the trek back.
Thanksgiving break proved to be a popular time for similar undergraduate teams and hobbyists launching high-powered rockets at the desert facility. On that late November weekend, OLVT joined teams from the University of California, Berkeley, and UCLA, as well as a number of individual groups at the Friends of Amateur Rocketry site.
Despite the season, temperatures reached the 70s during the day, and with little cloud cover, the sun was relentless in the desert. The team paid close attention to the weather conditions, as external factors such as high winds or an unexpected sandstorm can negatively impact the launch.
Schoner noted that the Friends of Amateur Rocketry facility takes pride in its organization and hyper-vigilance regarding safety. The facility provided bays for teams to set up and build, and launch rails were first come, first served. There was a wide range of launches scheduled for that Saturday, with a number of groups simultaneously waiting their turn for the launch pad.
Kevin Engel, who serves as OLVT co-president along with Preisser, remembered the anticipation felt by the team members on launch day. “One of the key things we tried to do was keep what is known as ‘rocket fever’ at bay,” said Engel. “That build-up of excitement and nervous energy can outweigh common sense if you let it get a hold of you. We tried to tone that down, and our preparation with outlining launch procedures really helped with that.”
Once ready, the team members found one group ahead of them, and anxiously waited approximately 30 minutes to load the Test Turkey onto the launch rail. All participants onsite were directed to take shelter in bunkers, and the safety officers announced OLVT’s launch over the communications system. The countdown began, and the group held a collective breath. With a thunderous roar and a flash of flame and smoke, the rocket lifted off.
Test Turkey hit 30,000 feet.
“The launch of our vehicle was successful,” said Preisser. “The motor worked properly, it left the ground, our parachutes successfully deployed, and we were able to find the rocket shortly after launch. After about three seconds, you aren’t able to see what happens to the vehicle in flight, so we rely on the onboard avionics and data collection systems for our results. While it didn’t quite make the height we initially predicted, many of the systems we wanted to test were a complete success.”
According to Engel, the Test Turkey landed about 1.2 miles away from the launch rail, and with the assistance of drones relaying live video back to the team, the students were able to walk into the desert and find the body of the rocket in a quick and painless recovery. While the launch itself overall was successful, the team took note of multiple areas for improvement.
After returning to Blacksburg, the team reviewed the data collected and examined the external factors leading up to the launch. While waiting their turn to get on the launch rail, their camera battery had died early, and their altimeters began logging data during that period, causing it to run out of storage space too soon. The motor did not burn as long as the team had expected, resulting in an altitude of 30,000 instead of 50,000 feet. In addition, the main parachute deployed a bit early, as the rocket was spinning, and caused some vibrations that had an effect on the shear pins that enclosed the chute. Always looking forward, the OLVT team sees these minor issues as teachable moments, and as points to improve upon in the future.
Opportunities for a wide scope of majors
In the spring of 2016, a group of 10 passionate engineering students created the OLVT team, which has since grown to over 90 members. Team members are undergraduate students of all skill levels from across the College of Engineering, as well as a handful of physics, chemistry, economics, and business majors. Through their involvement, the students gain valuable expertise in avionics, structural design, propulsion systems, launch safety, trajectory analysis, and business operations.
“I think we’re right in the middle of the next golden age of space flight,” said Schoner. “There are so many exciting missions happening and being planned within the next decade. When it comes to the future of spaceflight and exploration, the need extends beyond just engineers and astronauts; there will be people designing the flight suits, nutritionists, and computer science engineers working on simulations for landing on Mars. This next age is wide open, and there are lots of opportunities to be involved.”
Those opportunities include financial administration, as costs to manage and support a team and mission of OLVT's size are staggering. OLVT, along with a dozen or so undergraduate design teams, operates out of a bay at the AEDL under supervision of experienced lab managers. Fabrication of materials and development of various technology systems can be completed in-house, while other parts, such as the rocket motor and parachutes, are commercially outsourced. Traveling with a team of 20 and transporting the rocket and gear across the country can quickly take a toll on team finances.
Funds raised on Giving Day for the AOE department directly support the facility costs for the Advanced Engineering Design Lab, the makerspace that houses a dozen engineering teams including OLVT. The OLVT team also receives funding and support from the aerospace and ocean engineering department and the College of Engineering but primarily relies on fundraising and corporate sponsorships to help meet its objectives. Every student design team could benefit from a business and public relations arm, said Schoner, because the skills they are building have direct applications in the aerospace industry.
Over a year ago, Ron Poff, assistant professor in the Pamplin College of Business, came on board as faculty advisor for the OLVT business sub-team. Under his guidance, a small subset of students have gained practical experience on the business development side of the space business, through managing the team’s budget and fundraising efforts, implementing communications and marketing campaigns, and developing relationships with potential sponsors.
Looking ahead, the team plans to begin development of its next vehicle, the Hokie 0.75. According to Engel, one of the biggest impending changes has less to do with design or the technology systems on board and more to do with the fabrication process. The AEDL, which officially opened in March of 2020, did not exist when the Test Turkey was designed and built, meaning the team outsourced the creation of many parts and systems on board.
“For the Hokie 0.75 and future launch vehicles, we now have the benefit of utilizing the onsite machine shop and all the resources at the AEDL to build our rockets from scratch using raw materials,” said Engel. “We have access to 3D printers, filament winders to fabricate airframes and nose cones, and the water jet to cut machine precision parts out of aluminum. Not only will this drive the fabrication costs down, but at the end of the day we are giving our members the knowledge and experience they need to be successful in their chosen field of engineering.”
Both Engel, who recently graduated, and Preisser, who will complete his undergraduate degree in the spring, plan to stay at Virginia Tech to work toward their master’s degrees in aerospace engineering. Both agree that the OLVT team provided valuable field experience that fortified their educational path.
Preisser said his involvement with OLVT complemented his academic work in physics with hands-on experiential learning. “This has been an amazing experience,” he said. “It allows for a lot of variety, with the hands-on engineering work balancing out what I’m learning in the classroom and fueling my passion for both physics and aerospace engineering.”
After nine semesters on the team, Engel was elated to see the Test Turkey successfully launch to 30,000 feet in the desert just weeks before commencement. “OLVT gave me a platform to prove myself, and helped me gain the experience necessary to get into graduate school for aerospace engineering,” he said. “This team has a solid mission plan, and having a large, long-term goal has given members a purpose, motivating them to push each day towards something bigger.”
While participation on OLVT has reaped individual benefits, the experience also brought tremendous growth for the group as a team.
“It’s been a long road to this point, and I’m impressed with how far this team has come,” said Schoner. “In a short period of time, they have evolved from a couple of people into an organized team armed with knowledge and a plan. This group has taken the advice from mentors, faculty, and experts in industry, and they are progressing toward their goal in calculated steps. Most importantly, they’ve taken the time to learn, and the result is they have all gained a lot of valuable experience.”