Research seeks to break the mold of ultra-lightweight aerogels
Producing ultra-lightweight materials that are also strong could be a revolution across multiple industries. With groundbreaking work from an interdisciplinary team of chemists and 3D printing experts, that revolution could be closer.
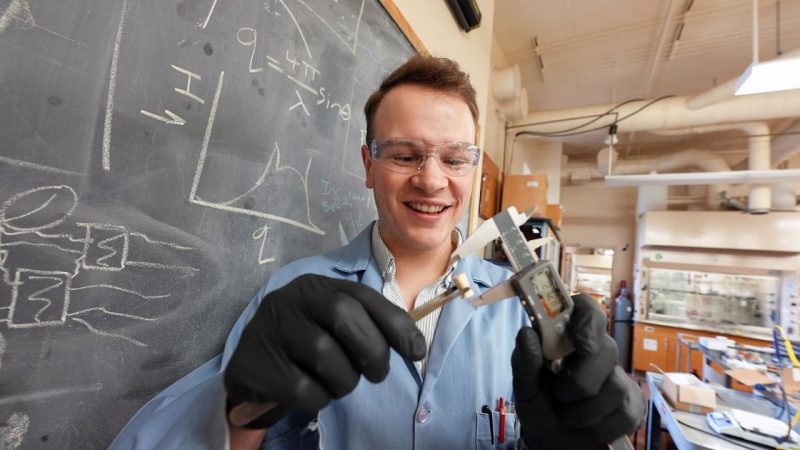
Aerogels are a unique class of ultra-low-density materials with a weight only about 15 times heavier than air. If an average adult were made of aerogel, they would weigh somewhere between 3 and 14 pounds.
The material has been around for a little less than 100 years, and the first aerogels were a highly porous solid containing more than 99 percent air, nicknamed “frozen smoke.” Although these aerogels made from silica glass have achieved the Guinness World Record for the lowest density solids, they are known to be very brittle and quite expensive to process.
Today, the race is on to find new materials and cost-effective methods to produce incredibly strong aerogels for advanced applications such as thermal insulation for aerospace vehicles, passive solar insulation for next generation housing, water and air filtration, lightweight packaging, controlled drug delivery, and personally tailored biomedical scaffolding.
That race has some strong Virginia Tech contenders. Robert Moore, a professor in the Department of Chemistry in the College of Science, has joined forces with Christopher Williams, the LS Randolph Professor of Mechanical Engineering in the College of Engineering. They have brought together the resources of both their groups to produce new approaches to engineered aerogels, channeled through the Macromolecules Innovation Institute. Graduate researchers Garrett F. Godshall and Daniel A. Rau have led those teams with innovations in both materials and machinery with the methods published in the journal Advanced Materials.
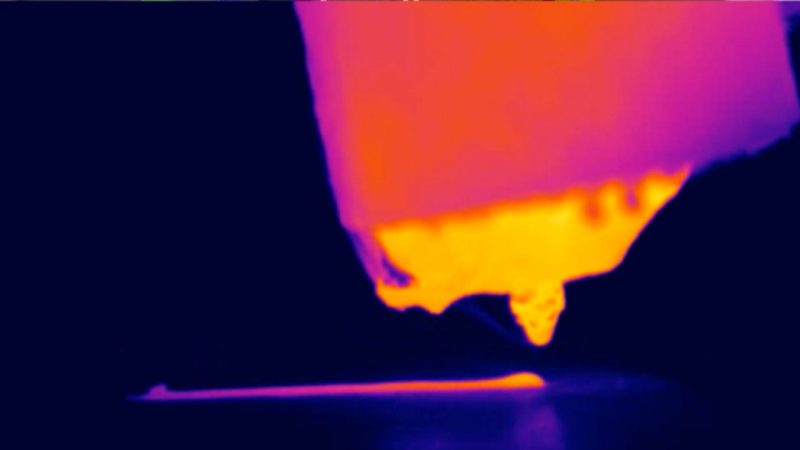
Strong, lightweight skeletons
The first step to making an aerogel involves producing a gel, a 3D solid network that entraps a liquid, like water in gelatin. The next step involves carefully removing the liquid in the gel, leaving behind a microporous sponge-like skeleton that is ultralight because the heavy liquid has been replaced by air and potentially strong because of its interconnected 3D lattice.
One material that had not previously been developed as an aerogel is polyphenylene sulfide (PPS), a super strong thermoplastic often used as a substitute for metal when weight reduction and chemical resistance is required. As an aerogel, PPS could usher in a new wave of applications, particularly in lightweight high performance thermal insulation. Recently, Moore’s research group has demonstrated a simple process for creating PPS gels and aerogels using a unique nontoxic, environmentally friendly solvent.
Moore’s team brought its process to Williams, who has pioneered novel 3D printing methods.
"Bob and I have been working together for many years thanks to the interdisciplinarity fostered through the Macromolecules Innovation Institute,” said Williams. “We hosted a joint meeting between our two groups over a summer so that our students could become more aware of our labs' capabilities and expertise and ideate ways we could collaborate. From that meeting, we identified that Bob's novel approach for synthesizing PPS aerogels would meld well with my group's expertise in 3D printing and prior work in printing PPS.”
“Unlike the silica aerogels or other crosslinked polymers used by NASA, our PPS gels don’t require complex chemical reactions and they can be melted and solidified over and over again,” said Moore. “All we have to do is make a hot solution of commercially available PPS and then cool it to room temperature. Using our new, safe solvent, which is actually an FDA-approved food grade additive, the PPS solutions gel in seconds. It is as simple as making Jell-O. But once we saw the super-fast solidification of these gels, we knew it was time to team up with the Williams group to see if we could print this stuff.”
The PPS aerogel barrier has been breached with Moore’s discovery of rapid PPS gelation. Using a combination of simple chemistry and 3D printing innovation, the first additive manufacturing of PPS into an aerogel is now a reality.
Breaking the mold
Like gelatin, the gels that are used to make aerogels are conventionally formed in open molds. This yields a solid form with limited size and shape. Making PPS aerogels with engineered shapes and geometries requires a combination of innovations in polymer chemistry and advanced manufacturing.
On Moore’s team, Godshall produced pellets of the PPS gel and placed them into a new, high temperature printing tool designed by Rau specifically for this task. Inside the nozzle, the gel pellets are re-liquified and extruded onto a substrate, where they cool and re-solidify.
After the print is finished, the solvent-containing gel part has the solvent removed through an exchange process and freeze drying, resulting in a PPS aerogel. This process enables the formation of microscopic pores that can be tuned by the print settings. Moreover, at the macroscale, the three-dimensional form of the PPS aerogel can be tailored by the infinite shape possibilities of 3D printing.
Creating large, lightweight shapes to the contour of an airplane wing or small insulating structures incorporated in electronic devices means a reduction of materials in manufacturing; strong aerogel frameworks could equate to a reduction of fuel with lighter vehicles, and engineered thermal insulators could advance energy efficiency in next-generation technologies.
"This publication represents a significant breakthrough in the manufacturing of complex aerogels from engineering polymers,” said Williams. “Bob's synthesis technique can work for a number of other high-performance polymers, and the printing process can be easily modified to account for these changes. We were surprised to learn that the processing conditions have an effect over the morphology and density of the aerogel structure. We are excited to study this further and discover how to gain control and program this structure and performance into new multi-functional parts."