Graduate student team wins award for innovative 3D-printed water filter design
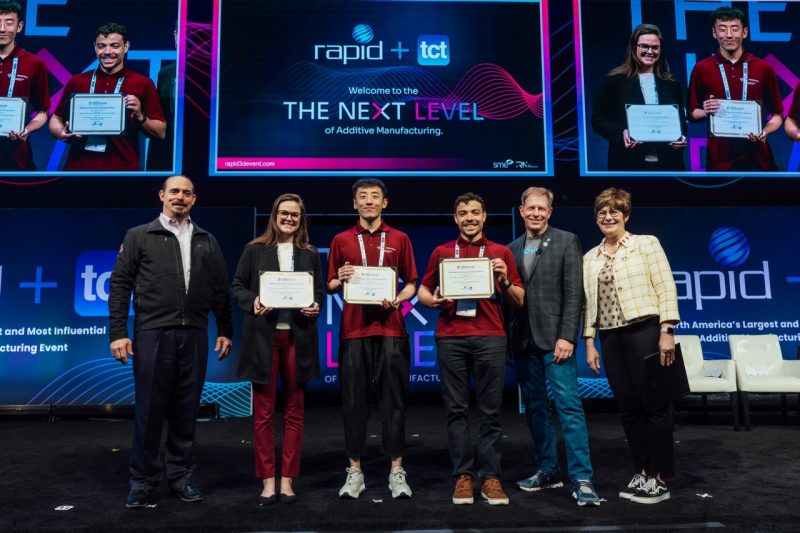
“Never in a million years did I think I, a chemist, would win an additive manufacturing award,” said Michelle Pomatto, a Ph.D. student in the Macromolecular Science and Engineering graduate degree program. Yet, Pomatto found herself on a team with two other students, Yiqun Fu and Daniel Alves Heinze, accepting the 2023 Society of Manufacturing (SME) Engineers Digital Manufacturing Challenge award.
Why did this award come as a surprise to Pomatto? Her work in polymer chemistry has largely focused on understanding the properties of a particular type of polymer known as an ionomer. To her, this seemed totally unrelated to additive manufacturing, which is a field of study that develops advanced processes and materials for 3D printing.
However, in fall 2022, Pomatto took an additive manufacturing course taught by Chris Williams, the L.S. Randolph Professor of Mechanical Engineering, as part of the macromolecular science and engineering curriculum. There, she teamed up with Fu and Alves Heinze, upon discovering that their complementary skill sets could offer just the right type of expertise to address the SME Digital Manufacturing Challenge while also satisfying the objectives of the class's final design project.
The SME Digital Manufacturing Challenge is an annual international competition that challenges student teams to develop solutions to large, complex problems using additive manufacturing. Unlike the 3D printing setups that some people may have at home for crafting small tools or trinkets, students leverage industrial-scale additive manufacturing processes that produce complex products from specialized materials, as is done in today's aerospace, automotive, and medical markets.
This year’s challenge was to design an additive manufacturing solution to a problem caused by natural disasters or emergencies. The team designed a handheld water filtration device that can be quickly made using additive manufacturing techniques and be deployed in after natural disasters, such as earthquakes or floods from torrential rains, have blocked access to safe drinking water.

As part of the team, Fu — advised by Williams — contributed the chemical engineering expertise he had gained as an undergraduate as well as what he learned in the graduate additive manufacturing course, to design the filter's complex shape and run simulations to predict how well the filter would perform. The filter design leverages the geometric complexity that can be achieved through the layered approach of 3D printing and features internal channels with changing tortuosity throughout the structure.
Meanwhile, Alves Heinze — advised by Michael Bortner, associate professor of chemical engineering — brought his skills in material characterization and processing to the table, tailoring the properties of the polymers used to print the filter and processing the polymer into filament for printing. And Pomatto — advised by Robert Moore, professor of chemistry — shared her deep knowledge of the polymer material itself, which is already used to make filtration systems but has not been extensively explored for additive manufacturing.
The combination of these skill sets allowed for the integration of an advanced type of material to the growing field of additive manufacturing to generate a design that could one day be used to save lives.
"The success of this interdisciplinary team reflects exactly what is needed to advance the state of the art of additive manufacturing,” said Williams. “Transformative change will only come when the process, the product, and the material are designed in concert - and that is exactly what this team has done."
The macromolecular science and engineering program is designed to foster this type of collaboration among students in different fields of study. The program is run by the Macromolecules Innovation Institute, which is dedicated to transdisciplinary approaches to grand challenges that involve polymers. By combining input from multiple areas of expertise, researchers can often dramatically boost the level of creativity, innovation, and impact of their work.
This team is the second macromolecular science and engineering team to have won this international prize – highlighting the program's ability to train students with the interdisciplinary skills required to solve tomorrow's problems.
“This award would not have been possible without the interdisciplinary environment of the Macromolecules Innovation Institute and our diverse team that combined chemistry, chemical engineering, materials science, and additive manufacturing,” Alves Heinze said.