Novel 3D printing process will use advanced materials to reduce waste and emissions in commercial vehicle industry
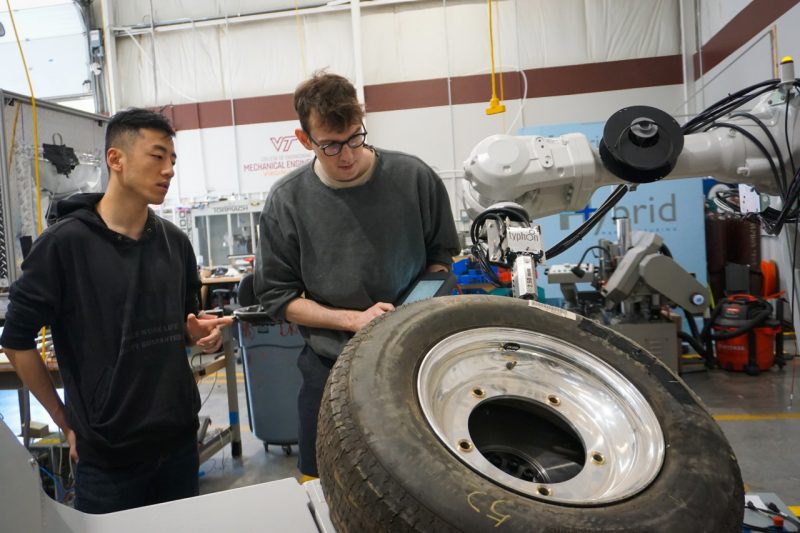
Chris Williams, the L.S. Randolph Professor in Mechanical Engineering, leads a team that was recently selected by the REMADE Institute for a $1.5 million project that will seek enhancements in the efficiencies of tire retreading.
Without the commercial vehicle industry, modern life would look dramatically different. We depend on vehicles such as tractor trailers for the transport of consumer goods, raw materials, and more. Given how resource intensive this kind of shipping is, increasing the efficiency of the entire system can be a big concern for industrial stakeholders and sustainability proponents alike. This is not limited to the fuel efficiency of the vehicles themselves, though. It also includes the materials used to keep the vehicles roadworthy — like tires — that play a surprisingly large role.
When a commercial vehicle’s tires wear out, they are often put through a process called retreading. The entire surface of the tire is buffed away, and a new layer of tread is adhered onto it. This ensures that the tire continues to perform safely, but still retains the majority of the material used to make the tire. In the U.S., about 14.5 million tires are retreaded each year.
Although this process results in less waste than completely replacing each tire when it becomes worn, there are still many inefficiencies in the system. Nearly 9 pounds of excess material are wasted per tire, and the retreaded tires could cause a drop in vehicle fuel efficiency, leading to additional greenhouse gas emissions when considered over a large scale.
This is where Chris Williams’s team comes in. With the recently awarded funding — which features a 1:1 cost share between the REMADE Institute and Virginia Tech — the team will pursue solutions to improve the efficiency of the retreading process.
“We are really excited to undertake this challenging project, which integrates advances in polymer science and manufacturing including 3D scanning, 3D printing, and industrial robotics,” said Williams. “If all goes well, the resulting retreading technology could result in annual reductions of about 90 metric kilotons of tire waste and 800 metric kilotons of CO2 [carbon dioxide] emissions across the retreading industry.”
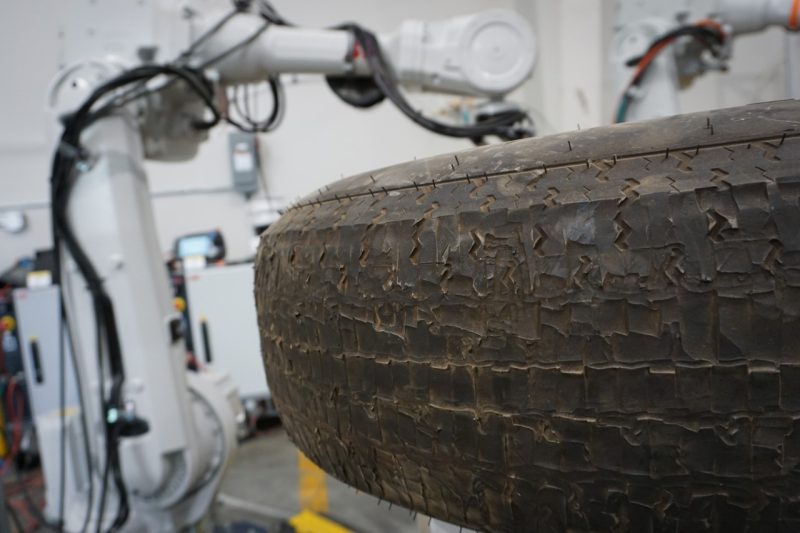
The REMADE Institute is a public-private partnership established by the U.S. Department of Energy and the first institute in the U.S. dedicated to accelerating the nation’s transition to a circular economy. With an emphasis on efficiency and waste reduction, a circular economy is a system that maximizes the reuse and recycling of materials.
REMADE Chief Executive Officer Nabil Nasr said the anticipated results of Williams’s project will move the U.S. closer to the nation’s energy conservation and emissions reduction targets, both of which have received renewed national attention recently.
The team’s approach will be to use 3D scanning technologies, new materials that can both be printed and resist the solicitations of commercial vehicle tires, as well as industrial robots that can print these materials only at selected locations around the used tires.
The development and evaluation of the bonding materials, along with the methods for applying and curing them on the tire, will rely upon team members’ experience in polymer science, which is a research area for which Virginia Tech is globally renowned. Williams is an affiliate of the Macromolecules Innovation Institute (MII), a hub for polymer science within Virginia Tech, that is known for its facilitation of interdisciplinary collaborations such as this one, bringing together engineering, chemistry, computing, and more.
“On behalf of MII, we are very proud that the REMADE Institute has recognized that this team of our faculty and students is uniquely skilled to take on the profound challenges of this project — from the basic science needed to create new materials capable of seamlessly mating with complex tire surfaces to engineering principles that will ensure durable tires that meet strict safety requirements," Robert Moore, director of MII, said.
In addition to the collaborators from Virginia Tech, this project will involve researchers at Arizona State University, as well as industrial partners at the tire manufacturing company Michelin. The global mobility company’s all-sustainable strategy includes a focus on the circularity of its products, a key benefit of retreading.
According to Williams, “The only way to address this project’s grand challenge of reimagining the tire retreading process is through a team-based transdisciplinary approach focused in simultaneous considerations of materials, the additive manufacturing process, and the final tires’ performance.”
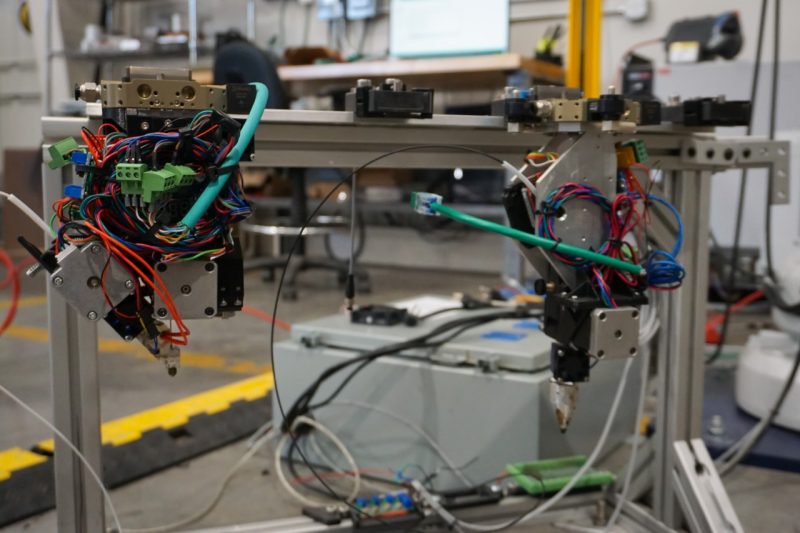
Tim Long, professor and director of Arizona State’s Biodesign Center for Sustainable Macromolecular Material and Manufacturing, will provide the expertise in synthesis of high-performance elastomers that are suitable for 3D printing. Michelin will bring the expertise in tire design and performance characterization as well as vision for industrial sustainability goals. Virginia Tech’s role will be to create a new manufacturing process that selectively deposits Long’s materials along the tire surface to meet the performance requirements of the tire industry.