Joint research team develops laser-optical technology to measure turbofan engine thrust
Researchers from Virginia Tech and Pratt & Whitney are working toward in-flight application of FRST, an optical instrumentation technique that is less intrusive and more cost-effective than traditional sensors and probes.
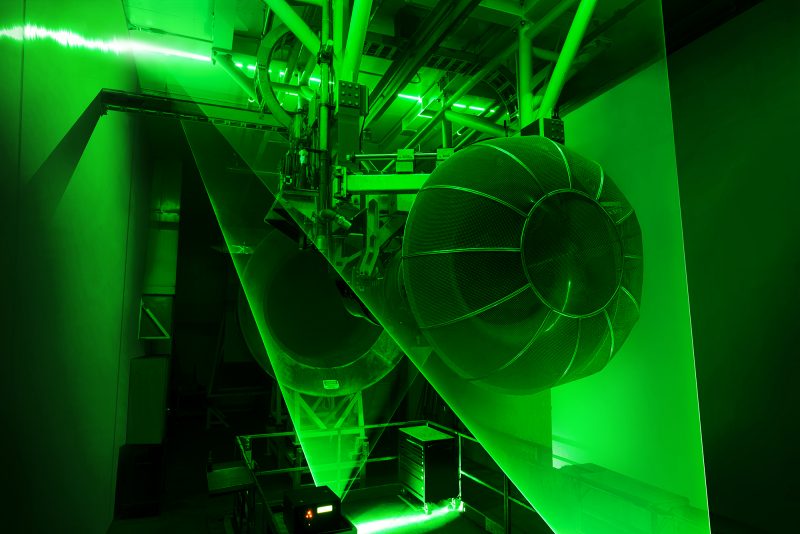
A longstanding industry partnership between Virginia Tech and Pratt & Whitney has resulted in a new technology that aims to revolutionize in-flight thrust measurement.
The pioneering technology calculates thrust using lasers to enable high fidelity measurement of key gas turbine engine parameters including velocity, temperature, and density. Known as Filtered Rayleigh Scattering for Thrust measurement (FRST), this new optical instrumentation technique offers significant advantages compared with traditional sensors and probes, which will support the development of more efficient engine core technologies and could enable the measurement of non-carbon dioxide particulate emissions in flight.
Researchers at the Pratt & Whitney Center of Excellence at Virginia Tech, directed by Virginia Tech Professor Todd Lowe, successfully measured engine thrust using FRST optical techniques on a research engine in a test stand, recording similar accuracy to that of traditional sensors and probes. The teams are working toward flight testing the technology.
“Though the principle of Rayleigh scattering has been known for centuries, Pratt & Whitney and Virginia Tech engineers have harnessed recent advancements in computing power, laser, and camera technology to demonstrate the first successful application on a turbofan engine,” said Lowe, professor in the Kevin T. Crofton Department of Aerospace and Ocean Engineering. “As we work toward in-flight demonstrations of FRST, we expect the technology will have other applications in the development and certification of aircraft engines.”
A patent-pending technology, FRST makes use of the ultraviolet light spectrum and relies on the principle that light scattering back from air molecules passing over a laser-illuminated area can provide information about the gas flow field, from which thrust can be derived. Applied to a turbofan engine, the light is provided by a laser beam directed across the turbine’s gas path while the resulting scatter is recorded by a high-performance camera and “filtered” for corruptions in the signal.
FRST optical instrumentation potentially eliminates the need for traditional sensors and probes, which can be difficult to install and cause flow blockage, particularly on smaller engine cores where space is limited. FRST also presents opportunities to measure non-carbon dioxide particulate emissions, which could contribute to industry wide efforts to understand and mitigate the environmental impact of those emissions, particularly with regard to contrail formation.
“The ability to use lasers and optical sensors represents a major step forward in engine instrumentation technology and is testament to the longstanding collaboration within Pratt & Whitney’s Center of Excellence at Virginia Tech,” said Geoff Hunt, senior vice president of engineering and technology at Pratt & Whitney. “FRST provides a less intrusive and more cost-effective method for measuring a range of engine metrics. We see exciting potential for FRST to help advance gas turbine propulsion technologies, particularly involving smaller and more thermally efficient engine cores, which are key to our next generation military and sustainable commercial engines.”
Pratt & Whitney and Virginia Tech have a longstanding collaboration in propulsion technology development with a focus on advanced instrumentation. The collaboration enables multiple graduate-level projects and internships at Virginia Tech and Pratt & Whitney, and research developed at the center is often transitioned to practice, directly impacting Pratt & Whitney products. The English-2-Engineering undergraduate program, housed under the center and focused on sustainability in aerospace propulsion, recently celebrated its first full year.