With instrumentation upgrades and modernization, Virginia Tech’s towing tank facility is primed for engineering research
Tucked away deep in the basement of Norris Hall, Virginia Tech’s 60-year-old towing tank was in desperate need of a face-lift. The basin and its towing carriage, primarily used for ship resistance research, was showing its age.
In late 2018, Associate Professor Christine Gilbert and Professor Craig Woolsey of the Kevin T. Crofton Department of Aerospace and Ocean Engineering secured $620,000 from the Office of Naval Research through the Defense University Research Instrumentation Program. The resulting instrumentation upgrade modernized the aging tow tank to provide Virginia Tech with a unique testing facility to perform innovative, nontraditional experiments that will serve the U.S. Department of Defense.
As one of a dozen or so academic towing tanks in the United States, the upgraded tank at Virginia Tech gives undergraduate and graduate engineering students valuable experience in state-of-the-art facilities, training on cutting-edge technologies, and ultimately the opportunity to work to advance military research, which plays a critical role in workforce development. The facility is located near several U.S. Navy and commercial facilities in the mid-Atlantic region, notably in Washington, D.C., and Norfolk, that regularly hire Virginia Tech engineers to support the Department of Defense mission.
Experimental towing tank facilities are used by naval architects and engineers to conduct physical model experiments in a controlled environment. While they vary in size and length, these facilities typically consist of a meters-long basin with a towing carriage mounted on rails above the tank, which pulls a model through the water at high speed. Researchers are able to test small-scale models of ships and ocean engineering vehicles and instrumentation, and capture data on hydrodynamics such as drag, lift, and force of flow while studying the effects that waves have on the vehicle's structure.
“Students are going to be able to use the new towing tank facility to gain foundational knowledge - whether they gain this opportunity through undergraduate or graduate research projects, independent study, and curricular or competitive engineering design,” said Gilbert. “The experience working on towing tank experiments at Virginia Tech is valuable job training for experimental work being performed in the field and at naval laboratories.”
Smoother movement, precisely controlled speed
Virginia Tech began working with DLBA (a division of Gibbs & Cox) in partnership with Edinburgh Designs on trade studies for the carriage upgrade starting in 2019. The former towing carriage was removed and has been replaced with a high-speed simple frame design that no longer requires researchers and students to ride on the carriage. The carriage is now remotely operated, equipped with cameras for monitoring, and boasts smoother carriage movement along its rails and a more precisely controlled carriage speed.
The carriage itself is capable of a constant maximum velocity of 7 meters per second (or 23 feet per second). The carriage is propelled with a belt-driven system with one large electric motor on each rail. The brakes are electromagnetic, providing enough braking force for the high acceleration and deceleration loads. The main structure of the carriage is constructed using ITEM aluminum extrusions in combination with large custom aluminum parts. These extrusions allow for the easy construction and modification of experimental setups.
Further additions to the towing tank include a dedicated data acquisition system and a suite of new sensors for experiments, such as force gauges, accelerometers, potentiometers, wave probes, inclinometers, and pressure sensors.
A newly installed vertical planar motion mechanism, designed by DLBA and constructed by Virginia Tech, facilitates controlled motion experiments for a model by prescribing heave and pitch motions. The mechanism, manipulated with two linear actuators, will have controllable heave motions with a range of 64 centimeters.
Although Virginia Tech’s Towing Tank is relatively small in size — the basin measures 98 feet long, 6 feet wide, and 4 feet deep — the maximum carriage speed is more than twice as fast as similarly sized tow tanks. The new upgrades to the facility enable precision measurements, making the facility well suited for small-scale ocean vehicles and platforms, including small craft, autonomous underwater vehicles, and biomimetic robots. Experimental capabilities include resistance and propulsion testing, linear and nonlinear maneuvering experiments, and seakeeping model development.
“Maintaining high-quality facilities to support formal and research-based education is essential,” said Gilbert. “In particular, the improved facility will help validate new analytical models for submerged vessels maneuvering in waves or computational fluid dynamics models for studying the slamming of small craft in waves.”
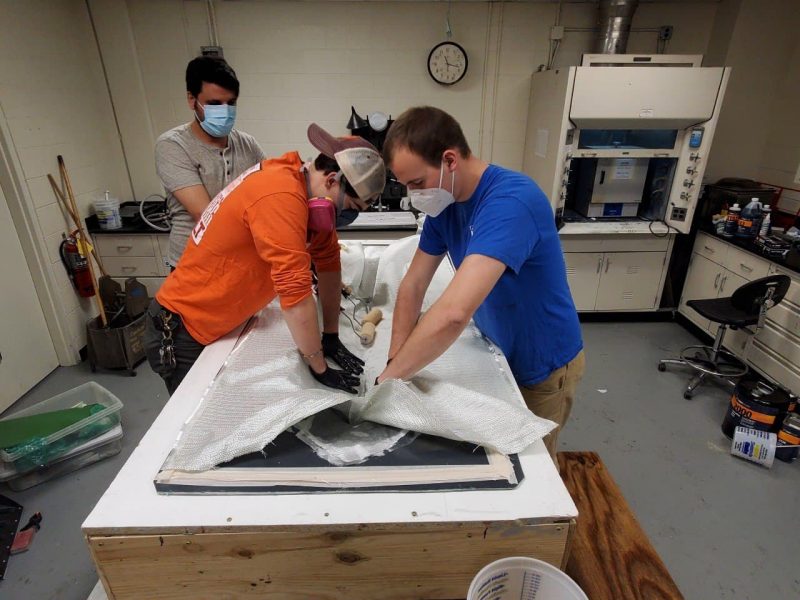
Slamming of high-speed craft in waves
The award is the result of a merit competition for Defense University Research Instrumentation Program funding conducted by the Army Research Office, Office of Naval Research, and Air Force Office of Scientific Research.
Gilbert, who also directs the Hydroelasticity Lab, is leading one of the first research projects to utilize the modernized facility, a study on the slamming of small craft in waves. Slamming occurs when a vessel, after being launched either partially or fully into the air by a wave, forcefully crashes back down into the sea. In addition to damaging the hull structure, risking the payload and instrumentation aboard, and injuring personnel, slamming events also can significantly limit operation and decrease performance of the vessel. Gilbert’s experiments will specifically focus on fluid-structure interactions between the hull and the waves.
In the upgraded towing tank, the research team will conduct controlled-motion slamming experiments using the generic prismatic planing hull (GPPH) model and a high-speed craft research shape made available by the Navy.
This current research expands upon one of Gilbert’s previous projects in which she collaborated with the United States Naval Academy on hydrodynamically loaded craft in waves. The model used in that study was rigid, so only the kinematics and pressure loading were measured.
Now, using the shorter length of Virginia Tech’s towing tank to their advantage, Gilbert and her team will model such slamming events in three phases of controlled experiments.
Gilbert and her team have been examining a cross section of the model, or a wedge, vertically dropped into calm water. Preliminary data was captured by performing vertical drops of the generic prismatic planing hull model into calm water at constant pitch angles. Her team plans to incorporate the forward motion and speed of the vessel, using the vertical planar motion mechanism to approximate a slamming event into calm water.
Finally, Gilbert and her team will replace a front section of the rigid model with flexible panels to take a closer look at the fluid structure interaction nd how the structure is able to respond to the impact. Just as a bumper on an automobile reduces impact during a crash, the flexible panels may reduce the slamming accelerations felt by those onboard the vessel during slamming events. This is of particular interest to the Department of Defense and the Navy, not only to improve human safety, but also to address slamming events in autonomous vessels. Slamming events that occur without personnel on board can negatively affect the vessel’s ability to continue on with its intended mission or the instrumentation’s ability to perform its functions.
Recent graduate Mark Shepheard '21, M.S. '22, who completed his master’s thesis under Gilbert’s supervision, collected and reviewed data from hundreds of slamming events and used machine learning to categorize them into three typical event types. Additionally, Shepheard performed vertical drop experiments on the generic prismatic planing hull model.
Moving forward, the team will be able to program those unique slamming characteristics into the vertical planar motion mechanism, isolate the motion, and run experiments under precisely controlled settings. In the towing tank, the team can force the motion of the carriage to exactly replicate those events and use it for validation against computational models.
This capability is unique to Virginia Tech, and positions the facility as one of few university-owned towing tanks able to execute high-speed, controlled-motion slamming tests with the vertical planar motion mechanism.