Feng Lin helps lead team asking, ‘How do we develop batteries with long life and fast-charging capability?’
The answer? Learn why they fail. Upfront: The properties of individual particles in the battery. Close behind: The network of particles.
Associate Professor Feng Lin, wearing a blue dress shirt and goggles, holds a pouch battery cell in his battery-testing lab at Davidson Hall. White in color, square in shape, the battery has two prongs sticking out of one side. Behind Feng is a rack with dozens of lithium-ion batteries being tested in charge cycles. Photo for Virginia Tech by Steven Mackay.
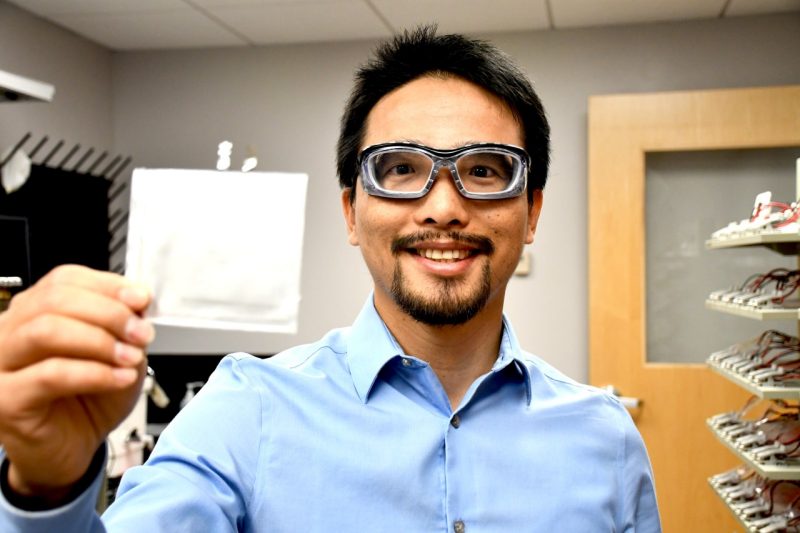
It doesn’t come on fast. It may take weeks to notice. You have the newly recharged lithium-ion AA batteries in the wireless kitty water fountain, and they last two days. They once lasted a week or more. Another round of charging, and they last one day. Soon, nothing.
You would be forgiven if you stood there and questioned your own actions. “Wait, did I recharge these?”
Relax, it’s not you. It’s the battery. Nothing lasts forever, not even the supposed long-lasting rechargeable batteries, be they AAs or AAAs bought in store or the batteries inside our cellphones, wireless earbuds, or cars. Batteries decay.
Feng Lin, an associate professor in the Department of Chemistry, part of the Virginia Tech College of Science, is part of a new international, multi-agency/university study published today in Science that takes a new look behind the factors that drive a battery’s lifespan and how those factors actually change over time in fast-charging conditions. Early on, the study finds, battery decay seems driven by the properties of individual electrode particles, but after several dozen charging cycles, it’s how those particles are put together that matters more.
“This study really sheds light on how we can design and manufacture battery electrodes to obtain a long cycle life for batteries,” Lin said. His lab is now working to redesign battery electrodes with the goal of fabricating electrode architectures that provide fast-charging capabilities and sustain a longer life at a fraction of today’s cost, as well as are environmentally friendly.
“When the electrode architecture allows for each individual particle to quickly respond to electrical signals, we will have a good toolbox to charge batteries fast. We are excited to implement the understanding to next-generation, low-cost, fast-charging batteries,” Lin said.
At foreground, Callum Connor, an undergraduate student in the Virginia Tech Department of Materials Science & Engineering, works with highly sensitive chemicals used in the creation of lithium-ion batteries. His work requires gloves, then long rubberized arms inside a sealed argon-filled workstation. Inside the tank, a third pair of gloves is required. Next to Connor is Department of Chemistry postdoctoral researcher Zhengrui Xu, who is also a co-author on the paper. Photo for Virginia Tech by Natalee Waters.
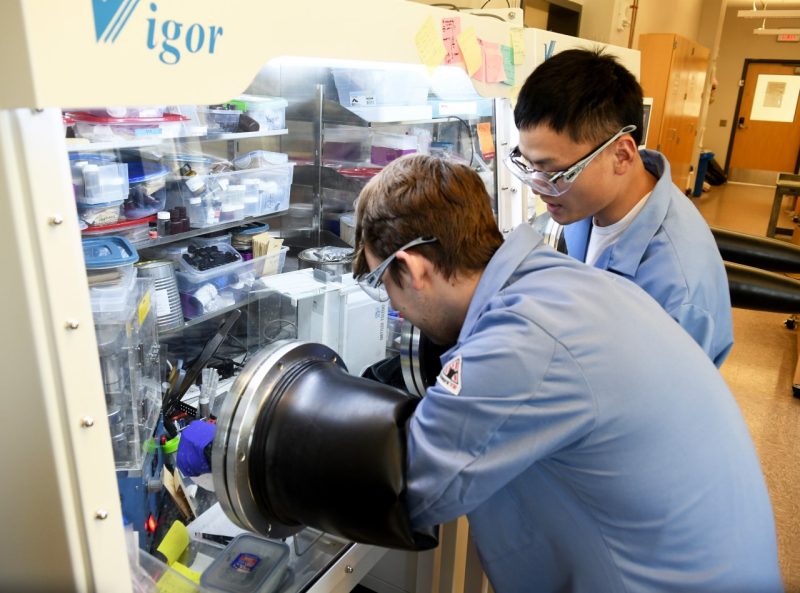
The study, for which Lin is a co-senior author, is in collaboration with the U.S. Department of Energy’s SLAC National Accelerator Laboratory, along with Purdue University and the European Synchrotron Radiation Facility. The Lin lab’s postdoctoral researchers Zhengrui Xu and Dong Hou, also co-authors on the paper, led the electrode fabrication, battery manufacturing, and battery performance measurements as well as assisted with X-ray experiments and data analysis.
“The fundamental building blocks are these particles that make up the battery electrode, but when you zoom out, these particles interact with each other,” said SLAC scientist Yijin Liu, a researcher at the Stanford Synchrotron Radiation Lightsource (SSRL) and a senior author on the paper. Therefore, “if you want to build a better battery, you need to look at how to put the particles together.”
As part of the study, Lin, Liu, and other colleagues used computer vision techniques to study how the individual particles that make up a rechargeable battery electrode break apart over time. The goal this time was to study not just individual particles, but the ways they work together to prolong — or degrade — battery life. The natural endgoal: Learn new ways to squeeze a little more life out of battery designs.
As part of its research, the team studied battery cathodes with X-rays. They used X-ray tomography to reconstruct 3D pictures of the cathodes of batteries after they had gone through different charging cycles. They then cut up those 3D pictures into a series of 2D slices and used computer vision methods to identify particles. In addition to Lin and Liu, the study included Jizhou Li, an SSRL postdoctoral fellow; Keije Zhao, a Purdue mechanical engineering professor; and Nikhil Sharma, a Purdue graduate student.
The researchers ultimately identified more than 2,000 individual particles, for which they calculated not only individual particle features such as size, shape, and surface roughness, but also traits such as how often particles came into direct contact with each other and how varied the particles’ shapes were.
Next, they looked at how each of those properties contributed to particles’ breakdown, and a striking pattern emerged. After 10 charging cycles, the biggest factors were individual particles’ properties, including how spherical the particles were and the ratio of particle volume to surface area. After 50 cycles, however, pair and group attributes — such as how far apart two particles were, how varied their shapes were, and whether more elongated, football-shaped particles were oriented similarly — drove particle breakdown.
“It’s no longer just the particle itself. It’s particle-particle interactions that matter,” Liu said. “That’s important because it means manufacturers could develop techniques to control such properties. For example, they might be able to use magnetic or electric fields to align elongated particles with each other, which the new results suggest would result in longer battery life.”
A member of the Macromolecules Innovation Institute at Virginia Tech and an affiliated faculty member of the Department of Materials Science and Engineering, part of the Virginia Tech College of Engineering, Lin added, “We have been investigating heavily on how to get electric vehicle batteries to work efficiently in fast-charging and low-temperature conditions.
“Beyond designing new materials that can lower battery cost by using cheaper, more abundant raw materials, our lab has also been working on understanding battery behaviors far from equilibrium,” Lin said, “We have started to study battery materials and their response to these harsh conditions.”
Zhao, the Purdue professor and a co-senior author, likened the degradation problem to people working in groups. “Battery particles are like people — we all start out going our own way,” Zhao said. “But eventually, we encounter other people and we end up in groups, going in the same direction. To understand peak efficiency, we need to study both the individual behavior of particles and how those particles behave in groups.”
The research was funded by the U.S. Department of Energy, SLAC National Accelerator Laboratory’s research and development program, and the National Science Foundation. The SSRL is a Department of Energy Office of Science user facility.
Citation: Jizhou Li et al., Science, date (DOI). This article uses content originated by Nathan Collins, science communications officer with the SLAC National Accelerator Laboratory.
Related stories
Chemistry’s Feng Lin Lab is splitting water molecules for a renewable energy future