Proof-of-Concept Program announces second year of funding to bring research to market
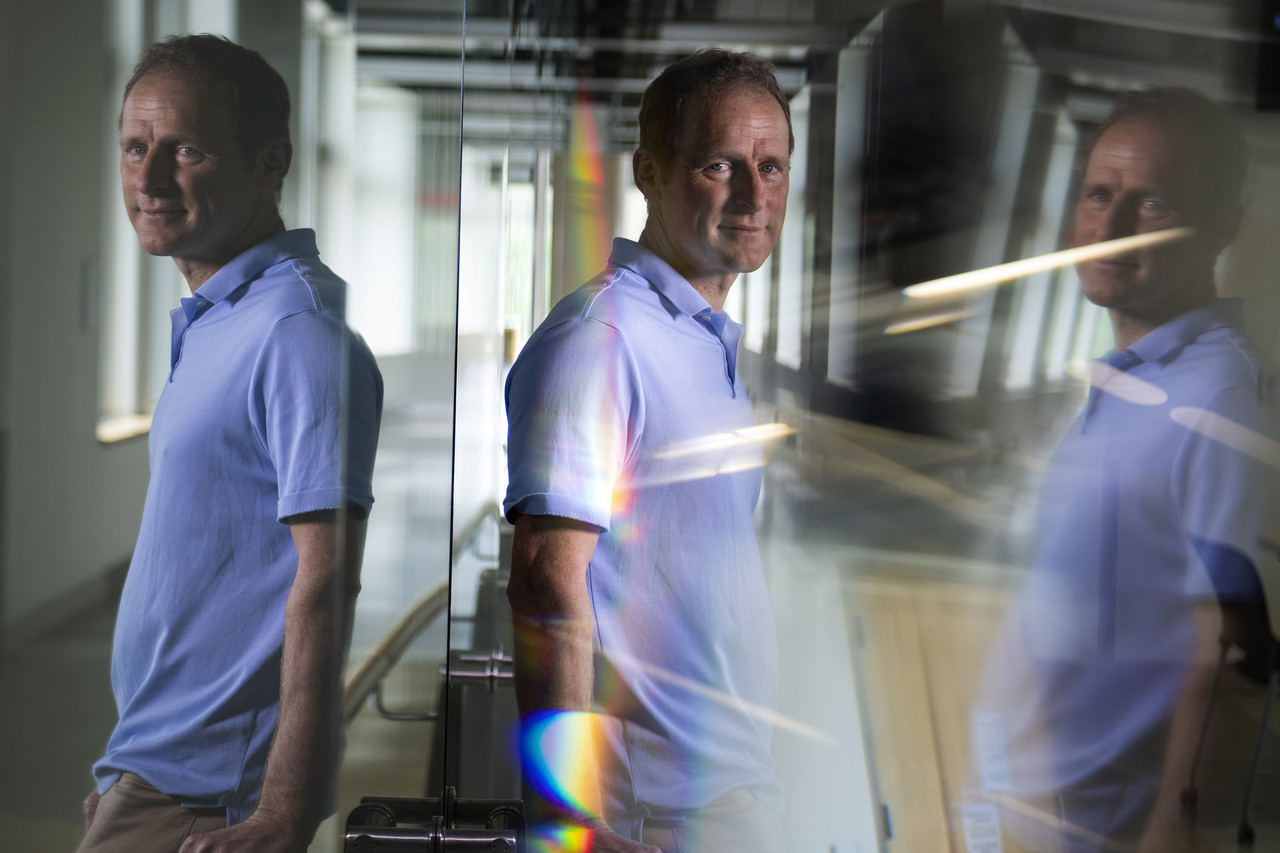
Just over a year ago, Virginia Tech Intellectual Properties (VTIP) with LINK + LICENSE + LAUNCH launched its inaugural Proof-of-Concept Program designed to help provide researchers paths to market for technologies from research with the potential for significant societal and economic impact.
Since then, more than $400,000 has been awarded in grants to Virginia Tech researchers to commercialize Virginia Tech intellectual property to license products, support startup companies pursuing commercialization, and develop early stage drugs.
“The first year of the Proof-of-Concept Program has been a great success and we are excited to be able to support Virginia Tech researchers and innovation into our second year,” said Mark Mondry who leads LAUNCH. “Selected projects receive funding and related support services to validate technology and market applications and attract future funding from federal Small Business Innovation Research and Small Business Technology Transfer grants, National Science Foundation I-Corps grants, seed funds, early stage private investors, and more.”
This fall, the program will initiate a third call for proposals with a deadline of Sept. 15, 2021. To learn more and apply, visit the webpage.
LICENSE and LAUNCH resources are housed within the Office of the Vice President of Research and Innovation and VTIP to help increase the value of these new technologies and propel them out into the innovation economy where they can make an impact.
In spring 2021, the following proof-of-concept proposals were awarded funding as part of the first year of the program:
Antimicrobial Coating
William Ducker, professor of chemical engineering, College of Engineering
Gary Whiting, Joseph H. Collie Professor in the Department of Chemical Engineering, College of Engineering
Ducker and Whiting have developed a novel antimicrobial film used to suppress transmission of microbial diseases, such as COVID-19, by continuously inactivating microbes on surfaces without human intervention. The funding will support early commercialization activities for antimicrobial coatings that can be applied to common-use surfaces, such as knobs, hand grips, service trays or a wide range of other articles. This technology offers numerous benefits over continuously disinfecting common surfaces manually using sprays, UV light, or other mechanisms. Subsequently, Ducker has formed a startup to pursue commercialization of this technology.
New Therapeutics to Prevent Malaria Resurgence
Paul R. Carlier, professor of chemistry, College of Science; director, Virginia Tech Center for Drug Discovery
Jopaul Mathew, graduate research assistant, Department of Chemistry, College of Science
Maria B. Cassera, associate professor of biochemistry and molecular biology, Center for Tropical and Emerging Global Diseases, University of Georgia
Approximately half of the world’s population remain at risk of malaria infection each year and current vaccines are only 50 percent effective. This reality necessitates drug therapy for those infected and as emerging parasites show increasing resistance to currently available drugs. This project is directed to early drug development activities for a therapeutic drug that offers a unique set of attributes to prevent malaria resurgence and potentially offer a cure for malaria itself.
Topology and Toolpath Optimization via Multi-Axis Material Extrusion Additive Manufacturing
Joseph Kubalak, postdoctoral researcher in the Department of Mechanical Engineering’s Design, Research, and Education for Additive Manufacturing Systems (DREAMS) Lab, College of Engineering
Christopher Williams, L.S. Randolph Professor in the Department of Mechanical Engineering, director of the DREAMS lab, College of Engineering
This project is directed to early stage commercial validation activities for a novel additive manufacturing process that incorporates custom toolpath planning algorithms that control a robotic arm to optimally align material depositions (roads) to the anticipated load paths to be experienced by the fabricated part. This process increases the mechanical performance up to 150 percent over conventional additive manufacturing methods and has potential applications in aerospace, automotive, prosthetics, and athletic equipment industries, among others.