Virginia Tech engineers victorious with another first place at agBOT
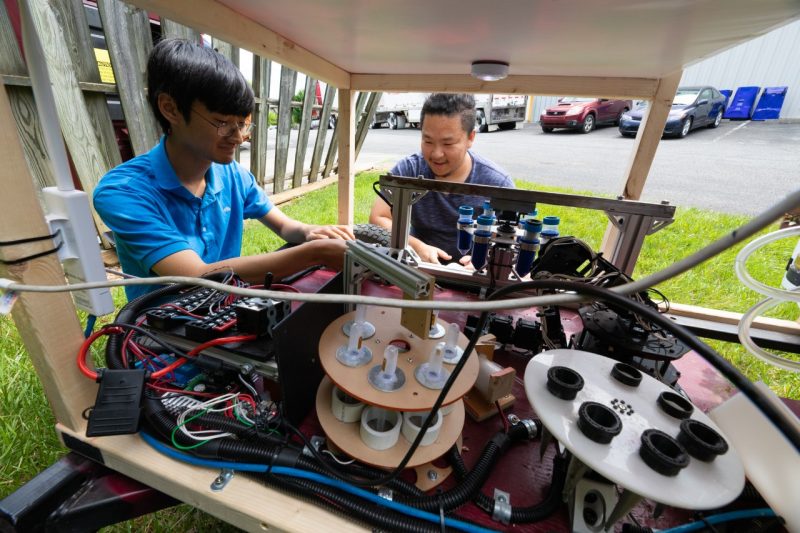
For the second time in two years, Virginia Tech’s agBOT student team came home from Indiana with a first-place trophy.
The 4th annual agBOT competition, hosted by Purdue University’s College of Agriculture and Gerrish Farms, was held in West Lafayette, Indiana, May 16-18. It consisted of two separate competitions: a weed and seed event and a competition to design an autonomous system that can collect, store, and prepare a soil sample for analysis.
The team, made up of 35 students from mechanical engineering, electrical and computer engineering, and computer science, all in the College of Engineering, were divided into five sub-teams.
Hongxu ‘Howard’ Guo, a spring 2019 graduate and a double major in mechanical engineering and electrical engineering, was the project manager and overall team lead. Guo said the project was important because soil sampling is a task traditionally done by humans who introduce errors into the collection by not having accurate location data and not taking samples at consistent depths.
“We created our vehicle to geographically tag sample locations to within two centimeters and our drill set for a consistent depth,” Guo said. “Also, traditional soil sampling takes weeks between collecting samples, sending them to labs and receiving the results. Using our system, it takes about 20 minutes to analyze each sample, and results are uploaded immediately to the cloud.”
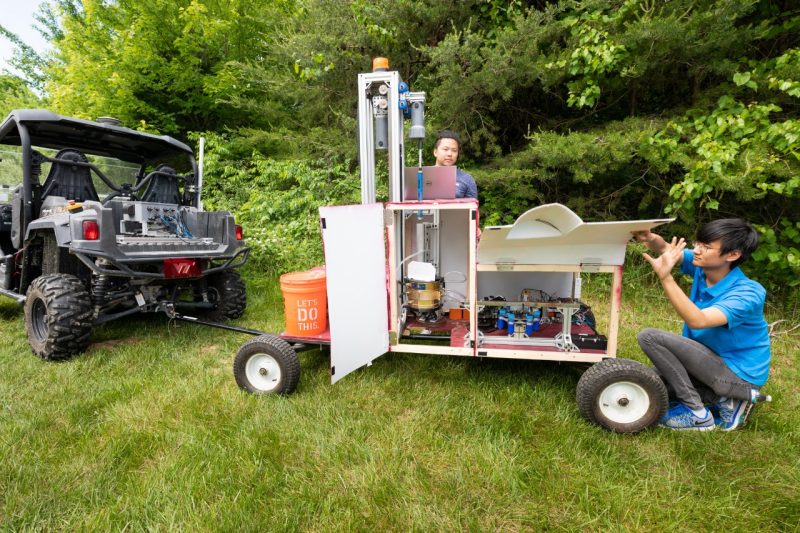
Working with faculty advisor Alexander Leonessa, professor of mechanical engineering, Guo and the team upgraded the autonomous ATV they used to win the watermelon harvesting challenge at agBOT in 2018 with obstacle avoidance technology and created a towed vehicle that was a self-contained laboratory.
“We went through several iterations of what we thought would work before putting this vehicle together,” said Guo. “We also consulted with Professor Jonathan Eisenback (School of Plant and Environmental Sciences in the College of Agriculture and Life Sciences), who has a semi-automated machine that tracks nematodes from the soil. We used that theory when designing and building our trailer, but we had to make our vehicle much smaller.”
After collecting a soil sample, a back-washing system extracts the soil from the drill and deposits it into a canister where it is run through a filtration process. A robot arm collects the filtered solution in a mesh tube and deposits the tube into a custom-made centrifuge that operates at 1,000 rpm.
“The tubes on the centrifuge are pre-loaded with a sugar solution that will separate the soil particle from micro-organisms,” Guo said. “Then the robot arm collects a pipette and takes the top layer from the tube in the centrifuge and puts it in a storage unit where the sugar is washed off, and part of the solution is picked up by pipette again and deposited onto a microscope slide. The filtration tower is washed between each sample to eliminate cross-contamination.”
Each team in the competition was given an automated microscope to use for the event. The solution is then analyzed by the microscope and result data uploaded to the cloud.
“The team did an exceptional job this year in understanding all the goals of the competition and working in multidisciplinary teams to create an exceptional vehicle,” Leonessa said. “They were the only team to complete all the requirements outlined by the organizers, who said their product was exactly what they were looking for.”
Written by Rosaire Bushey