Hybrid Electric Vehicle Team scores second place in national competition
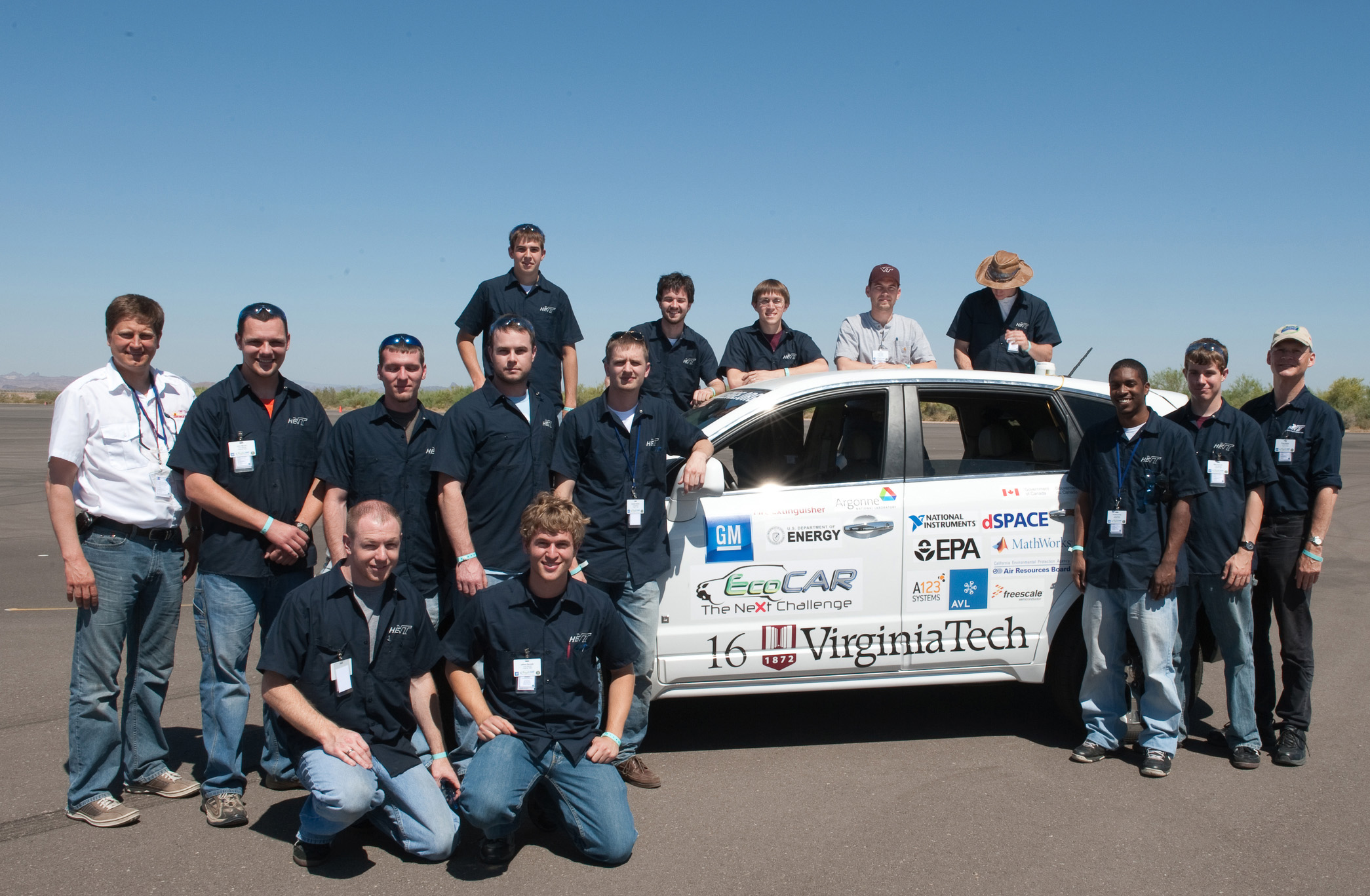
The Hybrid Electric Vehicle Team of Virginia Tech recently took second place in the international EcoCAR Challenge, a three-year design competition that seeks to inspire science and engineering students to build more energy-efficient "green" automobiles.
The Hybrid Electric Vehicle Team placed second behind Mississippi State University, with The Pennsylvania State University coming in third during phase two of the competition, according to Lynn Gantt of Yorktown, Va., team leader and a master's student in mechanical engineering. A total of 16 teams from across North America shipped their vehicle to General Motors' (GM) Desert Proving Ground in Yuma, Ariz., and then to San Diego for the two-tier vehicle testing competition.
The Virginia Tech team won: Second place overall, Best Electrical Presentation, Best Static Consumer Acceptability Presentation, Best Braking Distance, Best Lane Change, Best Use of National Instruments Tools, Best Progress Reports, Best Pre-competition Safety Tech Inspection, runner up on Lowest Petroleum Energy Use, and runner up for Lowest Tailpipe Emissions. In all, the team captured $10,000 in prize money.
The team was one of only three teams to complete all events at the competition, which is sponsored chiefly by the U.S. Department of Energy and General Motors. Based in the College of Engineering'sJoseph F. Ware Jr. Advanced Engineering Laboratory, the group is comprised of two graduate and 24 undergraduate students. Their 2009-10 academic year goal was to build a 65 percent production-ready vehicle by physically re-engineering a crossover SUV donated by GM in fall 2009, Gantt said.
"Our vehicle is now a combination of components from three different GM vehicles, plus a high-voltage battery pack system, battery charger, and two electric motor controllers," Doug Nelson, a professor of mechanical engineering and founding adviser of the Hybrid Electric Vehicle Team, in early May. "One of the big challenges is to keep a student-built vehicle safe, which is a main focus for the team, while learning how to control the vehicle for the best performance and fuel economy."
During phase one, in the 2008-09 academic year, the team was tasked with creating a virtual model of their re-imagined SUV that would improve fuel efficiency and reduce emissions, while retaining the vehicle's performance and consumer appeal. The team placed sixth during this phase.
The team received the physical car in fall 2009 and soon set to work on re-engineering it. The greatest change came under the hood of the car. Out went the factory-supplied V6 engine and corresponding transmission, and in went a 4-cylinder 2.4L GM ECOTEC engine and 4-speed automatic transmission.
Major changes included the spare tire compartment being readied for a 600-pound battery pack that holds power modules donated by A123 Systems Inc. The battery chemistry is Lithium Iron Phosphate LiFePO4 wired together to make a 360-Volt battery pack. With this, the car can travel 40 miles without turning the engine on, Gantt said. The car is now powered by grid electricity and E85 (85 percent ethanol and 15 percent gasoline) fuel. Other changes include a modified rear axle to hold a new electric motor; a new high-voltage air conditioning compressor, a DC/DC converter was added to make 12-volt power from the 360-volt battery pack since there is no room for a conventional alternator.
The team regularly consulted with professional engineers, including Virginia Tech alumni now working at GM, during the re-build process. While testing in Yuma, the team learned valuable information from GM employees, organizers from Argonne National Labs, and competing teams, Gantt said. This data will be applied to the vehicle as the team prepares for third and final phase of the competition.