University engineers began the paradigm shift in the manufacturing of power electronics products
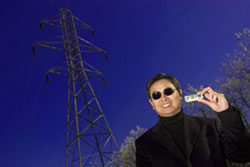
Some 12 years ago, Intel, a multibillion-dollar global company that increased its operating revenue by some 45 percent in 2007 alone, became such a fan of Virginia Tech's Fred Lee and his power electronics center that it asked his help in developing the next generation computer processor. By 2000, every Intel processor used a revolutionary power supply source, known technically as a multi-phased voltage regulator module (VRM) that Virginia Tech helped to develop.
Today, Lee said all manufacturers of computer processors use the multi-phased voltage regulator module concept because it is modular and scalable, allowing quick adaptation to the fast processor development with ever-increasing demands in data processing speed and power consumption. Furthermore, the solution enables the manufacturers of power electronics products to use more economical automated processes as opposed to the conventional custom design that necessitates a longer, costlier planning time.
“This particular technology has enabled the U.S. power electronics industry to continue maintaining its leadership role in both technology and market positions. It has enabled new job creation and job retention in the United States. Without this technology infusion from the premier power electronics program in the nation, CPES (Center for Power Electronics Systems directed by Lee), the U.S. power electronics industry would have lost its market position to overseas low-cost providers in providing the power management solutions to the new generation of microprocessors,” according to a 2007 Virginia Tech report highlighting this achievement.
To the average person, this type of technological improvement that breaks a typically complicated power processing solution and replaces it with modular building blocks with highly integrated solution had many consequences. It represented the beginnings of a paradigm shift in the manufacturing of power electronics products –– including motor drives for heat pumps, air conditioners, and other industrial and commercial applications. Also, power electronics is integrated with the microelectronics business, now Virginia’s largest industry.
“Almost everything a consumer touches has power electronics in it. It’s really an enabling technology that is not visible,” said Lee who holds a University Distinguished Professorship. As this “enabling technology” gains widespread acceptance, consumers will see a reduction in energy bills. Lee and the other researchers in the five-university consortium that comprises the Center for Power Electronics Systems, funded for 10 years by the National Science Foundation, believe they can reduce the world’s electric power consumption by 30 percent through their advances in power electronics.
“We are changing the way electricity is used,” he said. For example, if data centers, which use enormous amounts of energy, can be redesigned from the current AC distributed system, using off-the-shelf equipment, to a new power system architecture based on high-voltage DC systems, an initial study shows the efficiency could be improved some 10 to 20 percent. Web giant Google claimed that every one percent improvement in the efficiency of the data center means a $1 million savings in electrical energy bills, according to Lee who started at Virginia Tech in 1977.
“The long term health of the [United States’] power electronics industry has been of increasing concern with the migration of the manufacturing base to Asia. Most of the power electronics industries are bottom-lined focused and emphasize development rather than research,” Lee said.
“When they can spend 80 cents per hour versus $18 an hour per employee,” industry did not have the motivation to improve the technical aspects of the manufacturing process. But with globalization and the cyclical events in the economy, often attributed to the cost and heavy use of energy, the need to produce a savings in future power consumption becomes of paramount importance to every type of consumer and supplier, including the manufacturing industry.
Center for Power Electronics Systems researchers used the knowledge gained while designing the voltage regulator module to develop an integrated approach to power electronics systems. What they envisioned was analogous to a set of standardized toy building blocks (Lego). They would develop integrated power electronic modules (IPEM) as the basis for their new system approach.
The center’s integrated power electronic modules solution is based on the integration of a new generation of devices, innovative circuits, and functions. Similar to building blocks, the integrated soutions could then be customized and integrated into various solutions for specific needs. “We started the concept of integrated solutions,” Lee said, and “it is now a multibillion dollar industry.”
For example, Center for Power Electronics Systems researchers have patented numerous power electronic improvements, such as converters for hybrid fuel cells used in electric vehicles. They also hold several patents that can effectively reduce switch voltage stress and switching losses, known as zero-voltage switching and zero-current switching techniques. These underpinning technologies significantly reduce switching losses and stresses and form the basis for today’s high-frequency power conversion technologies widely used in the information technology industry, as well as aerospace, consumer, and industrial applications. They have a total of 50 patents, 131 invention disclosures, and 328 licenses issued by Virginia Tech Intellectual Properties.
As with the voltage regulator module technology, other companies have introduced systems similar to the center’s integrated power electronic modules, and the similar products are used to power the new generation of computers, telecommunications, and network equipment products. As the Center for Power Electronics Systems emerges from its National Science Foundation sponsorship, valued at more than $30 million, (and another $29 million from other sponsoring agencies), it is expanding its research mission beyond the power delivery and power management for the computer, telecommunication, and motor drives industries.
It is looking at efficient power management for small hand-held equipment, such as cell phones, PDAs, laptop/desktop computers, and to power architecture for such high power systems as data centers, more electric ships and aircraft systems. The center has set aside $1 million in the past two years to explore emerging power electronics technologies and applications using the future sustainable home as a platform to demonstrate potential energy savings and energy sustainability based on renewable energy sources.
“It’s an old argument,” Lee smiled. “Thomas Edison wanted DC but Westinghouse wanted AC. Well, we want to promote the DC voltage in energy-sustainable buildings. Specifically, the center’s researchers hope to design a future sustainable home that has load integrated power processors powering such loads as lighting, HVAC systems, entertainment, and data systems. The center advocates source-integrated power processors, which integrate power converters with solar photovoltaics on the roof and a dedicated wind turbine. The house would also have a bidirectional converter for a plug-in hybrid vehicle and for a grid connection.
Lee said he hopes that a “living lab” representative of a future sustainable home will be on the Virginia Tech campus soon.