Mechanical engineering professor uses coal to create 'wonder material'
Lightweight, strong, electrically conductive, and antimicrobial – graphene is a prime candidate for a host of applications. Now, a Virginia Tech team is making the material from a surprising source.

Since its initial discovery in 2004 by two professors at the University of Manchester, graphene has made a big splash in the scientific community. Its discoverers won a Nobel Prize in 2010 for developing the idea — then the race was on to find ways to produce and apply it. Roop Mahajan, the Lewis A. Hester Professor in Mechanical Engineering at Virginia Tech with a joint appointment in Materials Science and Engineering, has contributed a significant step forward in that race.
Graphene, often hailed as the “wonder material,” boasts unparalleled attributes — it’s 200 times stronger than steel, yet lighter than paper, and exhibits unique mechanical properties. At the microscale, it takes the form of hexagon-shaped lattices of carbon with a thickness of just one atom.
Because of its unique blend of properties, graphene could show up in many different places:
- It is strong enough to add damage resistance to the bodies of cars and planes.
- Formulated as an ink, the electrically conducive material can be printed on paper or clothing, opening the door to wearable electronics.
- Incorporated into batteries, it lowers charging time and increases power output.
- Its antimicrobial properties have a promising future as an antimicrobial agent.
- Made into a membrane, it could be used to filter water.
Mahajan’s team has been integrating graphene into existing materials and technologies to bolster their strength without adding a lot of extra mass, building a practical approach to leverage graphene’s unique properties. The effort has produced myriad innovative ways to incorporate graphene into everyday products, pressing the material to its full potential.
Getting greener and more cost-effective
Because graphene primarily consists of carbon, researchers must start with a material naturally high in carbon. Graphite, the primary component of pencil lead, is the usual choice because its composition is almost pure carbon.
Because graphene is a one-atom-thick sheet of material, producing it requires a significant amount of processing. The most popular technique is a modified version of an approach known as Hummer’s Method and uses sulfuric acid, potassium permanganate, sodium nitrate, and hydrogen peroxide at various stages. Three of those four chemicals are considered hazardous.
But Mahajan’s group has re-imagined a more sustainable method to source graphene not from graphite but from coal, dramatically cutting the number of harsh chemicals to only one: nitric acid. With fewer hazardous chemicals and less disposal to manage, this approach reduces the environmental impact as well as the risk to researchers.
Replacing graphite as the primary source for the material of the future comes with benefits. Most graphite is sourced from China, making its supply chain somewhat uncertain. Additionally, graphite is a critical ingredient in batteries, and the sharp increase in global demand for batteries has taken a significant bite out of that supply.
Although coal contains a lower percentage of carbon — 60 to 80 percent vs. a near-100 percent composition in graphite — the team’s less hazardous production method promises a better future for the environment. This shift could also open doors for a coal economy rapidly diminished across the globe, due in large part to its contribution to global warming when coal is burned.
In addition to the environmental benefits, there are economic bonuses. Mahajan’s method is less expensive than previous methods, creating a lower-cost supply that could spur new innovations in the market and help commercialization.
“Lowering the production cost of graphene is crucial to fully harness its exceptional properties and accelerate its broad adoption across diverse applications, potentially catalyzing the development of new markets and industries,” Mahajan said.
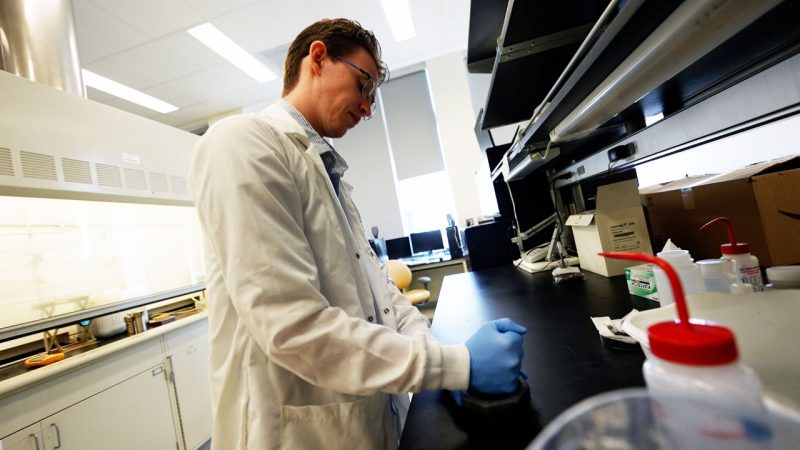
Grinders, marbles, and acid
In Mahajan’s unique process, the journey to synthesize graphene begins with the meticulous process of grinding down raw chunks of coal to create a coarse powder. The powder is put into a large cylinder that contains white marbles of different sizes, then rolled. The marbles grind and crush the dust, further reducing its size. The ball-milled powder is then chemically stripped of impurities such as metal sulfites and ash.
The ground and purified coal is then placed into a bath of nitric acid, which converts coal into graphene oxide. The acid is drained off and the unreacted carbon removed, resulting in graphene oxide powder, which can then be further converted to graphene by heat treatment. This is the substance that has been mixed with adhesives, silicon, glass, and metal to produce new kinds of composite materials for a variety of applications.
Mahajan’s team has demonstrated superior performance for coal against graphite-derived graphene. The groundbreaking work has resulted in a steady stream of publications, including one in the high-profile journal Carbon. This paper detailed the team's novel process and demonstrated the superiority of coal-derived graphene in the development of highly sensitive sensors to separate and detect single-stranded DNA aptamers. These sensors are widely used in diagnostics, therapeutics, food safety, and various industries because of their ability to bind to specific target molecules with high affinity and specificity.
The team in India
Expanding the understanding of both a novel material and a novel process calls for an expanded team, and Mahajan knew exactly where to turn, thanks to his leadership role in Virginia Tech’s global research footprint.
Mahajan is the director of strategic research and innovation for VT India, giving him a direct line for pushing innovation. This team of scientists, headquartered in Chennai, India, has been central to expanding the graphene enterprise.
That work produced a recent article in ACS Applied Nanomaterials focusing on graphene oxide’s role as a nanofiller in enhancing the mechanical performance of glass fiber-reinforced polymers. And the team is actively exploring other potential applications, including
- Wound healing solutions
- Wearable potassium-ion and urea sensors
- Corrosion inhibition of reinforced bars in concrete
- Technologies for green hydrogen production
While unfolding new technologies creates an exciting scientific environment, Mahajan is focused on more than just innovation. Reducing environmental hazards and boosting production on the “wonder material” carries a deeper implication: better quality of life for everyone. Smarter energy use, more reliable materials, and plentiful options for health care all rally to that cause.
“This wide spectrum of applications exemplifies the remarkable potential of coal-derived graphene technologies in reshaping industries and improving lives on a global scale,” Mahajan said.