Michael Bartlett receives NSF CAREER award to study soft composite manufacturing
Multiple innovative projects with soft robotics have established a strong body of work for the lab and helped lay the groundwork for future manufacturing methods.
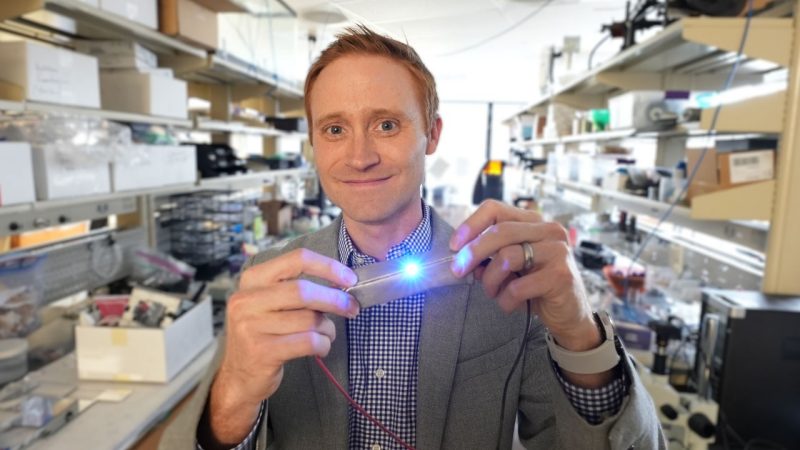
Michael Bartlett, an assistant professor in the Department of Mechanical Engineering, has been granted a $590,600 National Science Foundation Faculty Early Career Development (CAREER) award to research and understand new strategies for manufacturing liquid metal-based soft composites. These functional composites are deformable robust materials that could be used to make robots and electronics that are soft, stretchable, and compatible for skin-like wearable devices.
The CAREER award is the foundation’s most prestigious award for early career faculty, encouraging them to serve as academic role models in research and education and to lead advances in the mission of their organizations. This award follows Bartlett’s other notable young faculty awards, including the Office of Naval Research Young Investigator Award, DARPA Young Faculty Award and Director’s Fellowship, and 3M Non-Tenured Faculty Award.
Working with the robots we know
Bartlett’s team has an established record of innovative projects involving soft electronics and robotics, including a drone that morphs through meltable metal, a self-healing circuit, and an octopus-inspired adhesion glove. These innovations were produced as research-scale, single items in the lab, but they hold great potential for wider use.
Driving innovation in the field of soft robotics, the team is using its familiarity with the behavior of soft composite materials to create new approaches for large-scale manufacturing processes. To accomplish this, the researchers will continue studying methods of production in the lab and adapt those methods to be scalable.
“What’s exciting about manufacturing these materials is that you can completely change their properties through processing,” Bartlett said. “However, how to do this precisely is not well known. We aim to better understand how processing controls composite structure, so we can better enhance and tune properties.”
Manufacturing future for soft electronics and robots
Both the morphing drone and the circuit projects used a liquid-metal composite layer and required a process of deforming and reforming the materials to create their functionality. To determine how these composites might fit into a manufacturing method, the team will test new methods compatible with large-scale production, observing how liquid metal droplets evolve during processing. After those investigations yield their results, a new model for scaling up manufacturing will be developed.
“Liquid metals are unique in many ways, largely because they have the functionality of metals with soft mechanical properties like rubbers and liquids,” Bartlett said. “This is an exciting combination of properties and learning how to manufacture these systems can open new opportunities in soft material technologies.”
Once the team has created a scalable process to precisely control the mechanical, electrical, and thermal properties found in soft materials during processing, industries will be able to implement these methods and increase the availability of these new technologies. As new soft robotics continue to be developed and commercialized, manufacturers will be able to deliver rapidly evolving technology into the hands of a larger group of users.
As the researchers take a close look at the functions and properties of their materials, they will also be creating soft functional composites with unique properties, engineered by their findings to control the shape and connection of metal droplets during processing.
New technology in the hands of the next engineers
Outside the lab, the team will engage aspiring young researchers through a broader outreach program and day camp, which will particularly target first-generation students in Southwest Virginia in both K-12 and college. The objective in that offering is to engage, excite, and develop student interest and skills in manufacturing, soft electronics, and robotics while highlighting STEM career options.
“We are very much looking forward to this project not only to advance knowledge and technical capabilities in manufacturing soft materials, but also because we have a chance to encourage and inspire new engineers and scientists to work within this exciting area,” Bartlett said. “These materials are relatable as they are soft like skin yet can act like electronic materials, bringing together ideas STEM students see in their daily life.”