Learning Factory prepares students for Industry 4.0
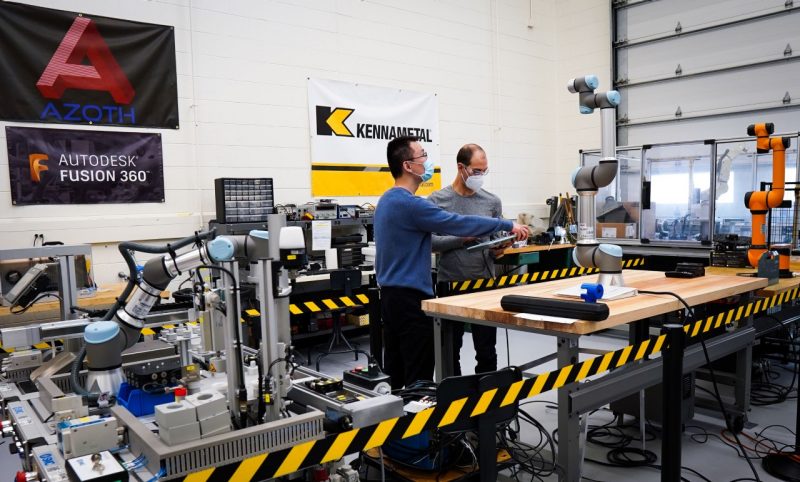
In the widget factory of yesteryear, most workers didn’t need an education beyond high school. They occupied the same station all day – cutting, ka-chunking, and assembling their piece of a process that required more brawn than brain to pound out the same widget over and over again.
But today?
Think robots, “cobots,” 3D printers, and “digital twins.” Think virtual dashboards and “4.0 technologies,” all wirelessly connected via the Internet and powered by solar panels in a net zero carbon environment.
So sophisticated and interconnected is the modern day factory – not to mention the widgets being created – that college degrees are often insufficient.
Unless your college is Virginia Tech that has its own Learning Factory.
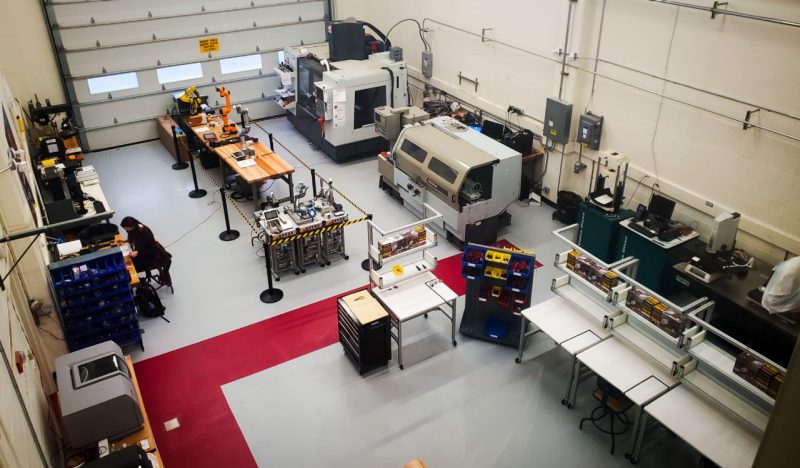
Launched in 2019 inside Durham Hall, the Learning Factory is housed within the Grado Department of Industrial and Systems Engineering. It’s a public-private partnership that provides Virginia Tech undergraduates a hands-on education of Industry 4.0, a term used to describe today’s manufacturing environment that incorporates smart technologies and the Internet to better connect and automate the industrial process.
Director Matt Earnest oversees the 1,800 square foot space which includes:
- A HAAS 5-axis machining center;
- An ECOCA CNC Lathe;
- A collection of robotic equipment that work alongside students--mobile robots or "mobots" (MiR 100 and Turtle Bot); collaborative robots or “cobots” (Aubo i5, UR-3, and UR-5) ; and, an industrial robot (Epson c3);
- An array of industrial Rize and Markforged 3D printers;
- An assembly system cell used to teach “lean” manufacturing principles;
- A control room featuring a virtual factory and digital dashboard that allows companies to simulate how new technologies could be incorporated into their facilities.
All this is fully powered by rooftop solar panels that generate a renewable energy source continually monitored inside.
“We believe we were the first net zero learning factory in the world,” Earnest said.
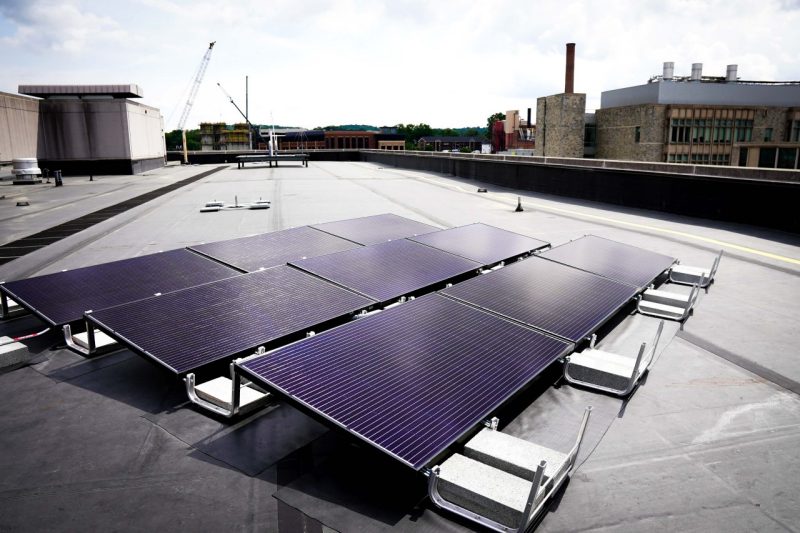
Bill Donohue, executive director of GenEdge Alliance – an organization that leverages federal and state funding to help Virginia manufacturers and businesses – invests $120,000 a year to fund Virginia Tech Industrial and Systems Engineering senior design projects conducted in the Learning Factory.
“The Learning Factory is really going to accelerate the development of students at Virginia Tech who can then move on to industries, help those industries adopt the new 4.0 technologies, and become more successful,” said Donohue. “So we’re very excited by this investment.”
One such student is Lilly Coleman, ‘21, whose senior design team used “open source software and some engineering elbow grease” to create a new data connection and monitoring system.
“By using the handbook we produced, we projected that a company could save an average of about 20 hours of programmer time in their connection automation [or] just over $8.3 million in potential time savings across the industry,” said Coleman.
“On a more personal learning note,” she added, “the understanding I was able to grasp of the importance of data has really helped me as I start my career. A lot of my current focus at work is on automating data sources and getting closer to real time analysis, so understanding the open source software and connection methods I became familiar with in the Learning Factory has given me a massive leg up.”
Likewise, the Learning Factory also serves as an incubator for companies to train existing employees and test new manufacturing technologies before investing capital – and disrupting assembly lines – to incorporate new equipment into their factories.
Scott Weimer, executive director of Roanoke Regional Initiatives, part of Outreach and International Affairs, supervises a $45,360 GO Virginia grant to help local companies embrace these technologies and address workforce training opportunities.
“We’re connecting employers in the region with the talent and resources at the Learning Factory to identify areas of potential collaboration. By listening to manufacturers and identifying their needs, the Learning Factory can develop workforce training programs that fill skills gaps among new and current employees and build an even more competitive workforce,” Weimer said.
In addition to GenEdge, the Learning Factory is sponsored by Moog, Northrop Grumman, Innotek, Association for Manufacturing Technology, Autodesk, Kennametal, Rize, SMC, Collins Aerospace, Azoth, Student Engineers Council, Solar Connexion, and Virginia Tech's Green Engineering Program.
Despite all its promise, the Learning Factory acknowledges the challenges of the Industry 4.0 world it is helping to shape.
The drive toward connecting individual machines and entire factories via the Internet and cloud computing has sparked the need for advanced cybersecurity to protect industries from malware attacks. It’s an area that’s providing Virginia Tech’s Department of Electrical and Computer Engineering with a real-world research opportunity.
And skeptics may view all the automation – the cobots and robots, 3D printers, and interconnectivity of it all – as a threat to human jobs.
But according to Donohue, “We have been trying to get companies to realize that we’re at peak employment now. Everybody is fighting for the same workers. We’re trying to get people to upgrade their skills from being just a welder to someone who can set up multiple welding machines and can do higher functions … someone who can become a more attractive employee and be more satisfied with their job.”
Someone who can not only build a better widget, but design it and oversee its entire production, using renewable power of course, from anywhere in the world.
Written by Michael Hemphill