A marriage of polymers and ultrasound

During an outdoor excursion in 2016, husband and wife faculty members Reza Mirzaeifar and Shima Shahab, both mechanical engineering assistant professors, batted an idea back and forth: What if they combined his work with polymers and her ultrasound research into a single project?
Since that hike, the pair have converged on a host of applications using this approach. They are working with a leading medical device company to fuel new innovations in noninvasive treatments, such as targeted drug delivery and surgical techniques. The project is moving forward with more than $510,000 in funding from the National Science Foundation.
The polymer portion of the work involves using materials with shape memory properties, or the ability to return to their original shape after they are deformed. A material’s return to its original shape may be triggered by temperature or some other external stimuli. In this case, the polymers are subjected to an ultrasound wave, prompting their restored shape.
Ultrasound technology is already widely used in medical applications such as diagnosis of gall bladder disease, viewing a growing fetus, and more. These familiar applications produce visual results on a screen as they pass through tissues, but sound waves can also be used to affect the properties of physical objects within the body. If these objects were made of a polymer, the ultrasound waves would cause a reaction in the polymer but cause no harm to the surrounding tissues.
Building on this idea, the couple combined the resources of both their labs to deform polymers and return them to their original shape using ultrasound waves. They found the theory to be viable, publishing their results in RSC Advances. Those early tests used samples of general polymers, subjected to standard ultrasound test waves, but the generic data proved to the researchers that the idea was worth pursuing further. The ultrasound did indeed cause a deformed shape to return to its original shape when subjected to the ultrasound, though the early test waves did not fully return the object to its initial shape.
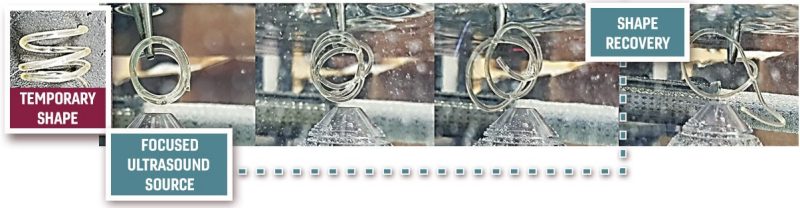
The next step was to be more specific in approach. Mirzaeifar focused on responses between more specific polymers, while Shahab observed the polymer response in an increasingly fine-tuned range of ultrasound frequencies. The results have proven very favorable, Shahab said, as their effort has yielded materials that return to almost 100 percent of their original shape.
“While ultrasonic waves can actuate any shape memory polymer, the recovery will be partial and slow,” said Mirzaeifar. “We target making a new class of shape memory polymers, which are particularly designed to be stimulated by ultrasonic waves.”
As the results became more promising, Mirzaeifar and Shahab approached Medshape, a company with experience creating patented medical devices. Founder Ken Gall and Basic Research Director David Safranski agreed to join the effort, giving insight into devices that might be created or enhanced with the new technology. With that guidance and their proven science, a proposal was submitted to the National Science Foundation under its Grant Opportunities for Academic Liaison with Industry program. The NSF responded with more than $510,000 to continue the research and pursuit of possible applications.
An early idea for such an application was targeted drug delivery. It could look like this: a container with drugs inside is injected or ingested into the body. Under normal circumstances, that container has enough drugs to both impact its target and also account for waste. A pill, for instance, has to have enough drugs to do the job it was intended for, but it’s also typically expected that some of the pill’s payload circulates to other untargeted parts of the body. In the case of this development, a drug container made of Mirzaiefar’s polymer could be deformed into a pill shape, but remain sealed and intact as it moved through the body. When the container reaches the area of the body that requires the drug, exposure to Shahab’s ultrasound waves cause it to return to a shape that open the container. In that way, drugs could be more strategically applied.
In addition to drug delivery, there is potential to apply the approach to stent treatment. If a polymer were 3D-printed into a cylinder but then compacted, it could be placed in an artery in its compressed form. When in place, administering the ultrasound waves to the object from outside the body would return it to its original shape, causing the shape to expand and open a clogged blood vessel. The list of possibilities grows from there.
By approaching the project from both their polymer and ultrasound research backgrounds, Mirzaeifar and Shahab have been able to more harmoniously engineer a holistic method that causes the two disciplines to function in a single, unified approach. Medshape’s continuing role is to ensure that the materials chosen for use are safe for medical use.
“This approach with ultrasound and polymers has the potential to revolutionize minimally invasive surgical techniques and inform new designs for implants and soft electronics,” said Shahab. “Working with world’s leading manufacturer of biomedical devices using shape-changing metal and polymer technologies will guide this fundamental research to solve critical industry needs.”
Further findings were published in IOP Science in October 2020.
Written by Alex Parrish