Engineering student takes third place in Boeing competition
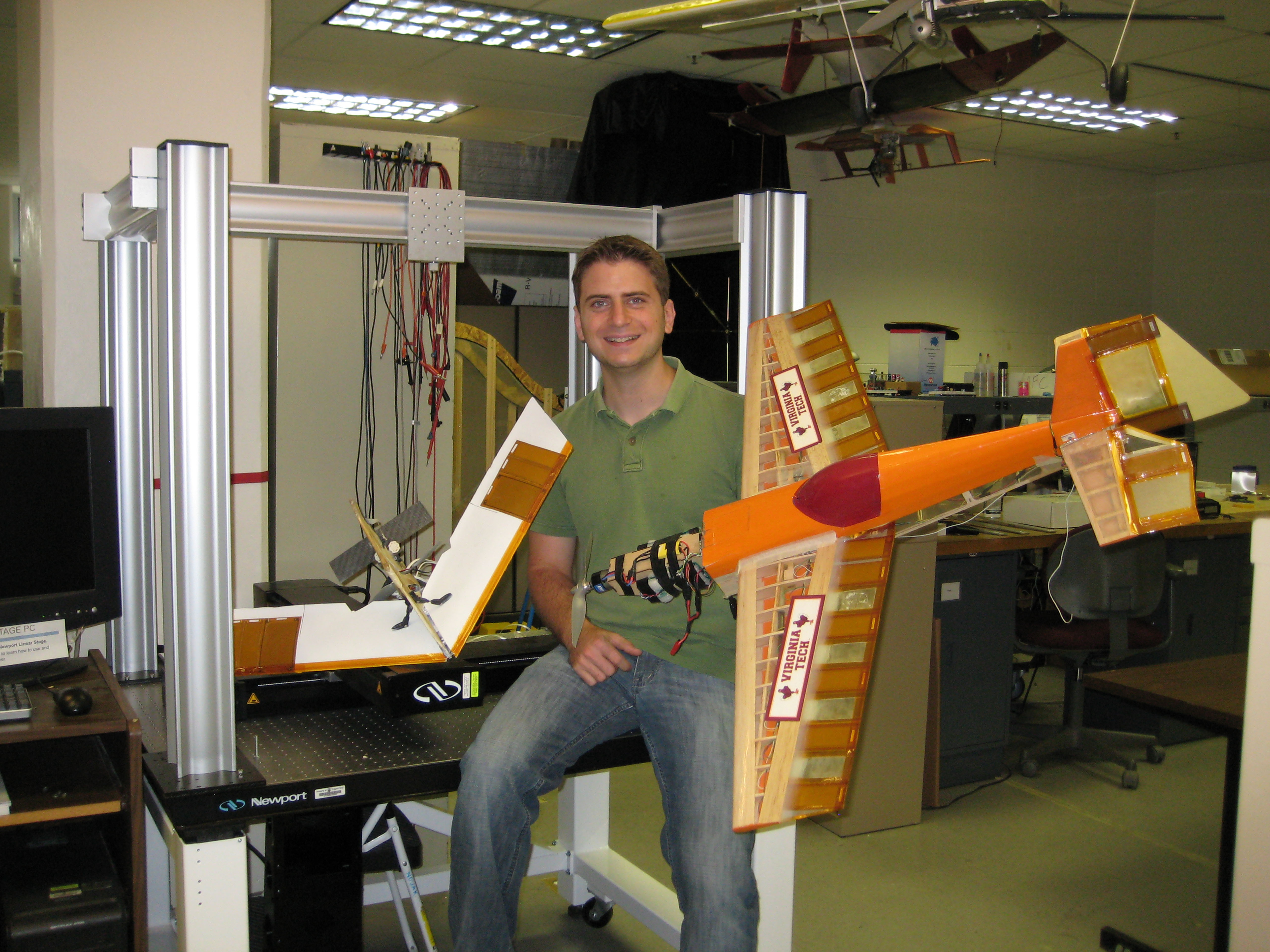
Onur Bilgen of Ankara, Turkey, a recent Ph.D. recipient in the mechanical engineering department at Virginia Tech, has won third place in the Boeing competition for Engineering Student of the Year 2010.
Bilgen, nominated by his adviser Dan Inman, who holds the George Goodson Professorship of Mechanical Engineering at Virginia Tech, is being recognized for his work to enhance the use of small, unmanned air vehicles and micro air vehicles. These vehicles have multiple practical uses, and the Defense Advanced Research Projects Agency first advanced research on this technology in the early 1990s.
The Boeing contest is open to engineering students worldwide, and its key criterion is the impact, or potential for impact, of the candidate’s work or future aeronautical or space technology. The entrant may be from an undergraduate or a graduate student.
Bilgen, Inman, and Kevin Kochersberger, also of mechanical engineering, recently filed for two patent disclosures on their work. One of the patent disclosures deals with a shape-changing airfoil, also referred to as a morphing airfoil. Kochersberger is the director of the Unmanned Systems Laboratory at Virginia Tech.
Specifically, the three have designed several novel airfoil concepts that provide aerodynamic control. An airfoil is the shape of a wing or it could be a blade that might be part of another component of the vehicle such as a turbine engine. The airfoil is typically used to generate lift in the aerial vehicles.
Bilgen, who is the lead author on the patent disclosure, says the airfoil’s uniqueness is due to its ability to change its shape or morph, much like a bird in flight. This specific airfoil uses piezoelectric actuators. Piezoelectricity is the electrical charge that occurs in certain solid materials due to a mechanical pressure. It also refers to the mechanical pressure generated due to the application of electricity. An everyday example for piezoelectricity might be the flame from a cigarette lighter when one’s finger exerts the mechanical pressure to cause the ignition.
Bilgen uses this electrical-to-mechanical conversion property of piezoelectric materials to change the shape of the airfoil. These actuators are placed at the top and bottom surfaces of the airfoil, and aid in the capability of the wing to change its shape depending on the electric voltage.
Bilgen studies the effects of several structural and aerodynamic parameters to achieve higher efficiency for generating lift while consuming as little power as possible. “Higher lift and lower drag can be achieved by using novel airfoils that employ piezoelectrics as opposed to conventional actuators such as bulky motors,” Bilgen added.
Earlier this year, Boeing announced Virginia Tech was one of its targeted schools for recruitment purposes.