Engineers design composite bracing system for injured Hokie running back Cedric Humes
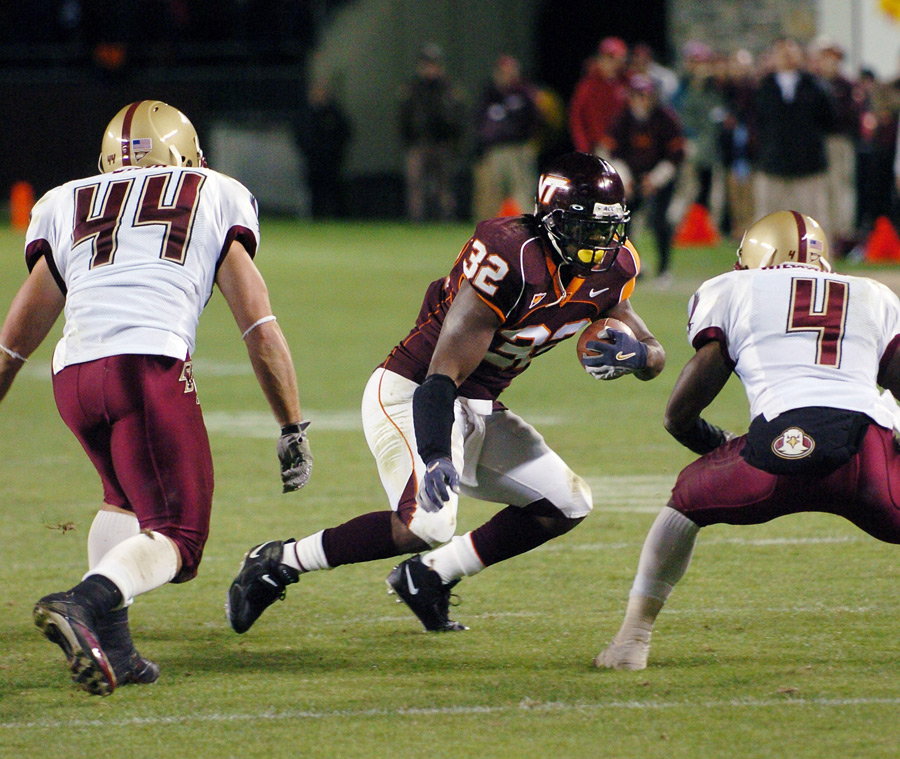
Virginia Tech’s starting running back Cedric Humes fractured his ulna, a bone in his arm, almost three weeks ago. Thursday night, against Boston College, he was able to play thanks, in part, to a prototype composite brace designed for him by Virginia Tech engineers.
Brian Love, a professor of materials science and engineering in the College of Engineering, and his biomaterials class met with Mike Goforth, Virginia Tech’s director of athletic training shortly after Humes’ accident. The engineering class offered to work on an alternate bracing system that they thought could provide a much stiffer support than the currently available polypropylene molded structure.
Among the suggestions considered by the engineers was a uniaxial polypropylene/carbon fiber composite sheeting made by the Fillauer Company (http://www.fillauer.com) of Chattanooga, Tenn. Since it was made from the same matrix as previously used bracing materials in medicine, the biomedical community was already familiar with the composite’s characteristics.
The company sent sample materials to Love, and the class was able to mold prototypes in their engineering laboratories. Then, the University hired a professional orthotist who completed one of the prototypes, and is working on the second. One consists of a bi-directional laminate and the second is composed of a uniaxial laminated composite.
The students reported their findings Tuesday to the Athletic Department—just two days before the Virginia Tech vs. Boston College game.
An added advantage to getting the design completed so quickly is that the biomaterials class is linked to the campus of the Wake Forest University School of Medicine. Virginia Tech spearheaded a partnership with this medical school in 2001, and formed the School of Biomedical Engineering and Science.
Love said, “The resulting stiffness and strength of the laminated structures has not been fully evaluated, but qualitative testing has shown that these structures are demonstrably stiffer than the current commercial devices already available.”
Love added that the new bracing system will be shared with the trainers at Wake Forest. Further bracing enhancements may evolve from the efforts of the students who may have developed even higher performing designs for the longer term than the commercial “off the shelf” solution.